浅谈非圆曲线薄壁零件数控车工加工工艺
摘要:在当现代社会中,非圆曲线薄壁零件在机械工业和日常用品中得到了广泛应用,在我国社会经济市场中占据着重要地位。究其原因,主要是因为它与其他类型的零件相比,具有造型美观、重量轻、节约材料和结构紧凑等特点,所以它成为我国各行各业中迫切需求的一种工业产品。但非圆曲线薄壁类零件由于壁薄、刚性差,以致加工时容易产生变形,不易保证加工质量。因此,在这种情况下,我们需要通过对非圆曲线薄壁零件数控车工加工工艺进行不断的分析,并采取可行性较高的措施,对该工艺进行合理的改进并完善,才能够降低其在生产中变形及质量问题出现的概率,进一步提高非圆曲线薄壁零件生产的效率。本文将针对非圆曲线薄壁零件数控加工工艺,对其进行较为深入的剖析。
关键词:非圆曲线;薄壁零件;数控车工;加工工艺
一、简析非圆曲线薄壁零件数控车工加工工艺的特征
虽然非圆曲线薄壁零件在我国各个领域当中都有着较为广泛的应用, 但是由于其具有比较低的刚性以及强度,所以在对其进行加工之时,也是具备较高的困难度的。如果从工艺特征的角度去进行剖析,其最大特点是壁较薄、刚性差,在加工过程中容易产生变形。因此分析其加工工艺的特征可以从两方面去考虑:第一是非圆曲线薄壁零件的变形表现,第二是减少加工变形的工艺措施。
(一)非圆曲线薄壁零件的变形表现
1.夹紧变形:因工件壁薄,在夹紧力的作用下容易产生变形,影响工件的尺寸精度和形位精度。
2.振动变形:因工件的刚性差,在切削力的作用下,容易产生振动而引起变形,影响工件的尺寸精度、形位精度和表面粗糙度。
3.热变形:因工件壁薄,质量小,热容量小,在切削热作用下易产生热变形,影响工件的尺寸精度。
(二)减少和防止加工变形的措施
1.工件分粗、半精、精车阶段进行。粗车时,由于切削余量较大,夹紧力稍大些,变形也相应大些;精车时,夹紧力可以稍小些,一方面夹紧变形小,另一方面精车时还可以消除粗车时因切削力过大而产生的变形。
2.合理选用刀具的几何参数。精车薄壁工件时,刀柄的刚度要求高,车刀的修光刃不宜过长(一般取0.2~0.3mm),车刀的刃口要锋利。
3.增加装夹接触面。采用开缝套筒或特制的软卡爪,使接触面增大,让夹紧力均布在工件上,从而使工件夹紧时不易产生变形。
4.采用轴向夹紧夹具。车薄壁工件时,工件尽量不使用径向夹紧,优先选用轴向夹紧的方法,靠轴向夹紧套的端面实现轴向夹紧。由于夹紧力是沿工件的轴向分布,而工件轴向刚度大,因此不易产生夹紧变形。
5.增加工艺肋。有些薄壁工件在其装夹部位特制几根工艺肋,以增强此处刚性,使夹紧力作用在工艺肋上,以减少工件的变形,加工完毕后,再去掉工艺肋。
6.充分喷浇切削液。通过充分喷浇切削液,降低切削温度,减少工件的热变形。
7.在中间可以安装中心架或跟刀架。车削薄壁工件时可以在中间搭一个中心架或跟刀架来提高工件的刚度,以防因切削力的影响而造成工件变形。
二、某一非圆曲线薄壁零件加工案例分析
为了更为直观的体现出非圆曲线薄壁零件数控加工工艺的过程及其效果,我们选取了如图1-1 的杯体类型的非圆曲线薄壁零件,对其数控加工工艺加以详细的说明。
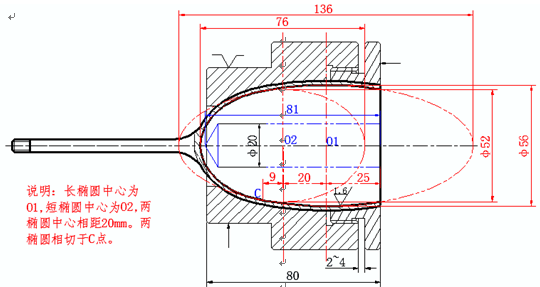
图1-1 某一非圆曲线薄壁零件
该零件的原材料主要是45#钢,根据图中所示的要求来看,加工该零件是具备一定难度的。其主要体现在两个方面:1)杯体壁厚仅为2毫米,生产批量过多,即使可以选用“撑内控装夹法”开展车削作业,但由于该零件的车削受力点与夹紧力作用点,这两点之间的间隔相距甚远,再加上其刚性不足,所以在加工中,极易出现晃动现象,容易变形。因此,在这种情况下就需要考虑杯体的加工定位问题,可以设计专用夹具进行装夹,以减少变形,提高加工质量。2) 该零件具备较高的精度,适宜选择“G76 和G92 合成法”,也就是“粗/细加工合成法”,对其进行两种层次上的加工,该加工法除了能够提高零件的精度之外,还能够降低非圆曲线薄壁变形问题出现的概率。
由于杯体壁厚仅为2毫米,刚性不足,加工时容易变形,因此,杯体的加工,要设计专用夹具进行装夹,以减少变形,提高加工质量。同时由于杯体内外轮廓均由椭圆曲线组成,因此不能用圆弧曲线近似代替椭圆曲线进行编程。具体加工工艺编制如下:
(一)整体结构特点及技术要求分析
该杯体属于典型的非圆曲线薄壁零件,外轮廓由两个外形左端由两个椭圆相切光滑连接而成,内轮廓同样由两个椭圆相切而成,且为内凹形,内壁底部为椭圆曲面,无退刀孔。M6螺纹与轴心线的同轴度为φ0.02mm,曲面光滑过渡,不能有振纹,同时要求细长轴无锥度或弯曲。
(二)加工步骤方面的分析
零件外轮廓光滑过渡无接痕,且尺寸精度和表面粗糙度要求高。因此,外轮廓的加工,安排粗、精车两个工步。首先粗车外轮廓,接着精加工外轮廓,精加工的余量应尽量均匀。为减少杯体变形,加工杯体内轮廓时要装夹在专用夹具上,而且刀尖半径应尽量小并保持刀具的锋利,同时要保证刀具的刚度,避免加工过程中出现振动。
1. 装夹棒料毛坯,规格为φ70×200,加工初始点为平端面,车端面钻中心孔。
2. 采取“G73封闭法”,“斜进式”进刀实现粗加工效果。粗精车零件外形φ6、R15、M6至尺寸,粗车椭圆外轮廓。
3. 以“循环式”进刀实现精细加工的效果,精加工椭圆外轮廓至尺寸要求。
4. 借助夹具,实现装夹效果,车削内轮廓椭圆曲面。钻φ20mm工艺退刀孔,钻孔深度81mm,加工杯体内椭圆轮廓。
5. 检查确定各项参数。
(三)切削用量选择的分析
当我们在对“切削用量”进行选择之时,可按照以下列表去进行,详见表1-1。
表1-1用刀具及切削用量明细表
步骤 序号 基本条件 主轴的转速范围(r/min) 进给的速度范围 留精车余量的范围(mm)
1 外轮廓粗车 1100~1300 F100~F150 0.3-0.5
2 外轮廓精车 1100~1200 F30~F45 无
3 内轮廓粗车 500~600 F100~F150 0.2-0.3
4 内轮廓精车 1100~1200 F30~F45 无
从上表中,我们可以看出:精车外内轮廓时,它们是没有设置“留精车余量”的。内轮廓精车时,将进给速度的范围严格控制在F30-F45中,能够在最大限度之内降低零件表面的粗糙程度;而在外轮廓精车中, 虽然其设定的进给速度以及主轴的转速范围均和内轮廓精车是相同的,但是它的作用却是用来达到“一次性走刀加工”目的的,以进一步提高零件加工的质量与精确度,由此加工出来的非圆曲线薄壁零件能够更加符合企业的生产以及消费者的使用要求。
三、结束语
综上所述, 本文通过对某一非圆曲线薄壁零件数控加工工艺的详细剖析,深度了解到加工工艺的步骤及其“切削用量”的选择要求,并通过合理设置进给的速度与主轴的转速范围,达到提高“切削用量”选择的准确性与有效性, 从而有效改善了该非圆曲线薄壁零件数控加工工艺中常见的质量问题、变形问题以及精度偏低问题,并为我国各大非圆曲线薄壁零件生产企业后期的生产工作提供了主要依据。
参考文献:
[1]周敏,魏加争.一种薄壁零件数控车工加工工艺[J]科技创新导报,2011,(12):37-37
[2]陈旭东.机床夹具设计[M].北京:清华大学出版社,2014(2).
[3]周晓宏.数控车削加工[M].北京:中国劳动社会保障出版社,2011.
[4]金福吉.现代制造技术----数控车铣技术[M].北京:机械工业出版社,2012.