基于振动监测技术在旋转机械故障诊断中的应用
摘 要:旋转机械故障诊断中通常采用振动监测技术,同时利用综合计算机技术、可编程技术、虚拟仪器技术等来展开旋转机械故障监测工作,并利用现代化手段分析设备运行中产生的振动信号,便于实现多通道信息采集。旋转机械在运行中,主要依赖于故障诊断系统,在防范故障隐患的环节,作业人员利用故障故障诊断系统,有效的排查设备运行中的安全问题,采用振动参数作为设备运行状态的主要指标,及时找到振动参数的共性,掌握旋转机械故障诊断工作的关键。
关键词:振动监测;旋转机械;运行过程;故障诊断;技术运用
Application of Vibration Monitoring Technology in Fault Diagnosis of Rotating Machinery
Qu Haijun
(Jiangsu Institute of Safety Technology, Xuzhou, Jiangsu 221011)
Absrtact: Vibration monitoring technology is usually used in fault diagnosis of rotating machinery. At the same time, integrated computer technology, programmable technology, virtual instrument technology are used to carry out fault monitoring of rotating machinery. Vibration signals generated in the operation of equipment are analyzed by modern means to facilitate multi-channel information acquisition. In the operation of rotating machinery, it mainly depends on the fault diagnosis system. In the link of preventing hidden trouble, the operators use the fault diagnosis system to effectively check the safety problems in the operation of the equipment. Vibration parameters are used as the main indicators of the operation status of the equipment. The commonalities of vibration parameters are found in time, and the key to the fault diagnosis of rotating machinery is grasped.
Key words: vibration monitoring; rotating machinery; operation process; fault diagnosis; technical application
前言
旋转机械运行中时常出现问题,鉴于这种情况,管理人员对技术人员提出更为严格的旋转机械操作技术要求,对故障检测技术的要求也提高了。为提升故障诊断效果,需要积极了解旋转机械工作现状及故障诊断技术的原理,以此为基础,增强对振动监测技术的认知,促进故障诊断工作的顺利进行[1]。加强振动监测,遵循标准化的故障处理措施,主动排查旋转机械运行中可能出现的隐患问题,积极了解故障问题的主要类型及发生的原因,总结成功的故障处理经验,以此推动振动监测技术在故障诊断环节的运用。
1.旋转机械的相关介绍
旋转机械运行中主要有微机控制和自动控制这两种方式,自动控制型的旋转机械具有成本低廉、可靠性高、操作便利、速度快等优势,工作人员可借助自动控制机械对转子不平衡进行自动调节与控制,但必须要在平衡装置过临界转速的情况下进行,无法在全转速状态下自动调节平衡[2]。可靠性是旋转机械运行中的关键,要更高的提高设备的安全性,要对转子部分进行高精度平衡,在惯性作用下让转子主轴与旋转机械轴重合,以此方式防止旋转机械运行中振动严重。
2.旋转机械故障诊断中振动监测系统原理
振动监测系统是集传感技术、网络技术、采集技术等为一体,日常工作中是采用一体化模式监测旋转机械运行中的故障,并排查安全隐患。技术人员在故障诊断环节,采用振动监测技术,利用测振系统将信息采集、存储等相应信息经过网络系统发送至用户终端,最终由用户终端专用软件来分析故障问题[3]。用户终端依据设定的预警系统依次检测旋转机械运行中的振动是否超标、是否存在设备损坏等问题,在此环节,专家分析软件快速得出某台机械振动超标及机械损坏等信息,做到防患于未然,并通过设置报警界线,对各个机械设备的运行情况进行科学分析和预警。
3.旋转机械运行中常见故障
运行中旋转机械产生了较大的振动,机械的运行频率、幅度、方向等发生改变,如果不及时采取措施,将引发重大的安全事故。
转子不平衡:旋转机械运行过程中,转子轴心质量分布不合理,运作中产生附加惯性力,作业人员操作不当,由于惯性力增加,转子运行中出现了故障。转子材质不合格,比如在安装环节,输送介质携带的附属物粘附在转子叶轮上,不平衡量沿着转子、叶轮轴向、径向等任意分布,惯性离心力增大,超出限制,从而导致运行中振动幅度和频率发生了改变[4]。
转子不对中故障:轴承安装底座安装不合理,转子轴运行中产生了预负荷,转子轴中心线发生偏移,转子高度不对中,由此引发轴承附加的负荷、转子附加力等增大,轴承还需要对负荷进行再次分配,这样一来,不仅对轴承造成损伤,还导致旋转机械振动猛烈,引发安全隐患。
摩擦故障:旋转机械运行中的摩擦故障有内摩擦、动静摩擦、外摩擦等几种常见形式,运行频率故障还伴随有高频分布的特点,低频成分中含有高次谐波。长时间的运行导致轴承产生裂纹,在垂直方向上的横向裂纹不对称,频率不稳定,机械振动严重。比如内摩擦故障:机械在负载作用下产生变形,单元件变形量增加,重新排列晶粒的环节,分子还需消耗很多能量,无法顺利地将所有的输入能量全部释放。材料内摩擦严重,加载金属材料环节会消耗比卸载环节更多的应力,致使机械振动强烈[5]。外摩擦:轴承与叶轮的固定不稳,高强度的作业环境中,旋转机械转子弯曲变形,同时长时间的运行导致叶轮与转子之间的摩擦力增大,位于叶轮圆盘接触面上的转子轴逐渐向两边滑动,内摩擦又一次增大,轴新的横向力产生弯矩。转子动静接触摩擦:转子运行中,轴承密封间隙小、润滑度不够,这都是造成转子热弯曲加剧的主要原因之一,旋转机械振动不规则,转子失稳,局部摩擦过大导致某一旋转机械严重损坏,其运行频率超出标准。
4.故障诊断振动监测系统设计
总体设计:合理设计故障诊断振动监测系统,科学设计数据采集卡,采用正规厂商生产的多功能数据采集卡,其性能参数采用8路差分输入法、16路单端输入,采样工作频率可达到250KHz,如下图所示为振动监测系统总体框架设计,作为参考。
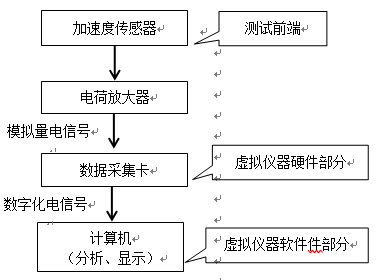
图1:振动监测系统总体框架
旋转机械运行过程中产生的故障问题,与各个部件的组成有关,由于系统内预设了多个通道,便于实现对机械不同部件的转子、轴承、等参数信息作出实时掌握,将从传感器接收到的电路信号以电量形式输出,同时依靠高频滤波器和数据采集卡,将系统内监测到的信息快速传递至计算机系统,便于网络系统对其进行高效处理[6]。下图为振动监测中采集系统的硬件组成。
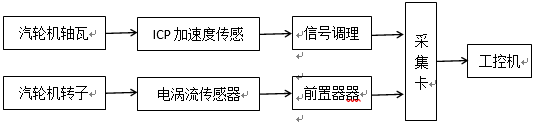
图2:振动监测中采集系统的硬件
软件系统设计:振动监测系统软件可分为采集控制、信号处理、故障诊断这几个模块内容,利用功能强大的计算机设备实时接收并输入各种信号波形,提高了数据采集及处理速度,保证了故障诊断信息的准确性和全面性,并发挥出可靠性高、实时性等明显优势。信号控制:利用信息采集卡实现系统内监测数据的双向数据通讯,首先作业人员从数据采集卡上读取相应的数字信号,将其及时存入数据库,然后利用分析模块进行信号与数据的分析与处理[7]。采集过程中,技术人员利用8测试通道,实现单通道、多通道实时采集,另外技术人员也可将虚拟仪器作为采集中的助手,以此发挥出采样多通道频率信息的重要作用。
信号处理:信号处理的关键是在线分析、离线分析、波形分析等,各个部分密切配合的情况下可实现信号实时分析与处理[8]。状态检测的主要作用是实时监测系统运行状态,能够进行在线监测和状态分析,通过借助监测参数掌握设备振动信号的特征值,监测结果主要分为安全、超限、危险这几种主要形式,其对应的系统显示颜色为绿色、橙色、红色,作业人员在分析系统监测故障的环节,主要采用模糊识别法和统计识别法,并配合逐项比较法和综合分析法来诊断系统故障信息,形成故障特征列阵图,提取多个频段信息,这是系统振动特征参数向量的主要控制内容,在此环节,可全面掌握系统故障机理。
数据处理中的注意事项:在数据处理中,技术人员要根据实际情况来分析数据处理中的关键内容,及时分析转子的振动状态,加强频域分析,便于进一步增强故障诊断能力[9]。分析时域波形,利用时域波形来了解转子的运行状态,科学的判定机械设备振动值是否超标,利用计算机网络系统了解采集通道的峰值和波形。借助计算机网络系统了解转子质量不平衡、油膜滑动、摩擦等状态,利用电涡流传感器采集转子运行信息,经过滤波处理的过程后,及时绘制转子运作轨迹,以此成为转子运动状态的主要监测依据[10]。信号分析是时域分析的主要内容之一,采用自相关函数分析不同时刻系统监测信号之间的关系、信号频率成分、波形状态等,明确两个信号的关系,利用多通道监测机械振动特性,同时为系统故障处理工作提供科学的参考。
5.旋转机械故障诊断中振动监测技术的注意事项
技术人员日常工作中对旋转机械运行状态进行定期监测,运用旋转机械之前,先观察其外观是否完好、存在损坏,同时利用网络系统测试旋转机械内部功能是否完好,确保机械设备功能完好后方可投入使用。比如认真检查气管口与压缩机的连接是否正确,利用焊条将回气管与压缩机连接好,将旧的过滤器更换掉,利用先进工艺从压缩机管口向内部依次施压,将压缩机的运行压力控制在0.8MPa。使用肥皂水检测系统的泄露情况,检测中发现气泡较多,于是技术人员及时放掉氮气,对冷凝器、回气管与压缩机的连接部位进行重新焊接,使其焊接牢固,焊接好之后再次采用肥皂水测试系统泄露情况,将肥皂水测试泄露的过程进行重复操作,直到无泄露出现为止。为防止设备损坏,加强对轴承的管理,轴承的好坏直接影响工作效率,为避免旋转机械在运行过程中产生剧烈振动,也为防止噪音,密切关注轴承装配不当、水分侵入、润滑不良等问题,对于损坏的轴承及时更换掉,并做好轴承更换登记。加强风机振动监测,规范电机运行,规定电机转速为1480RPM,电机功率为YB250M4,统一风机型号B47212NO,将风机风量控制在50800m/h左右。在压缩机管口安装压力真空表,采用耐压型胶管来连接真空泵,将系统的真空抽取干净,最佳的时间为1个小时,从而将旋转机械运行中的压力控制在合理范围内。待真空抽取干净,将真空泵撤走,立即关闭压力表阀门,同时接上制冷剂钢瓶,当真空充注量达到80%,及时停止充注操作,启动压缩10分钟后开始进行试机,在此环节检查管口是否堵塞、系统运行温度是否正常,待系统温度检测正常方可进行封口处理。
6.常见故障振动监测诊断及处理
转子不平衡故障的诊断:某旋转机械设备轴承箱表面振动强度为14.3mm/s,轴向振动强度13.9mm/s,垂直振动强度达到11.8mm/s,水平波、垂直波均为正弦波,根据振动波形判断此次故障为转子不平衡故障。利用振动监测系统对转子进行动平衡状态监测,严格遵照标准要求将转子上各个部位的小零件安装好,将松动的零件及时利用螺栓固定好,使其稳固。认真清理转子表面,对有污垢的部位进行及时处理。为保证转子不平衡故障处理的及时性,管理人员要制定有效的旋转机械故障振动监测处理措施,以此来约束作业人员,认真做好转子的清理工作,按照制度要求,加强对转子各个部位的有效检修,仔细检查各个部位的零件是否稳固,是否存在污垢,有无松动的情况,严格执行故障振动监测处理制度。对于出现异常的旋转机械,立即停机检查,做好安全防护,采用专业技术将损坏的转子及时更换掉,保证转子故障问题处理的及时性,更好的发挥振动监测技术的优势,下图为旋转机械故障振动信号采集过程示意图,作为参考。
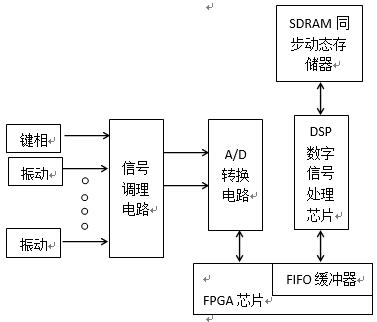
图3:旋转机械械故障振动信号采集
故障诊断中运用振动监测技术的案例:某旋转机械故障诊断人员,为及时排查减速器运行故障,及时对其进行振动信息监测,展开振动故障测试。主要对减速器各个轴端的振动情况进行科学检测,在此环节获取以下测点的振动速度信息:电机内风扇轴承振动速度3.200mm/s,齿轮轴承振动速度2.142mm/s,减速器输入端振动速度2.357mm/s,第二轴左端轴承振动速度0.653mm/s,第二轴右端轴承振动速度1.225mm/s,第三轴左端轴承振动速度1.124mm/s,第三轴右端轴承振动速度1.084mm/s,输出端轴承振动速度0.556mm/s。
转子不对中故障诊断:为保证转子不对中故障诊断的有效性,技术人员先了解这个故障的振动敏感参数,如下所示为:转子不对中故障振动敏感参数统计结果。
表1:转子不对中故障振动敏感参数统计
序号 敏感参数 随敏感参数的变化程度
1 振动随转速变化 明显
2 振动随油温变化 有影响
3 振动随介质温度变化 有影响
4 振动随压力变化 不变
5 振动随压力变化 不变
6 振动随负荷变化 明显
解决转子不对中故障时,首先分析故障原因,然后有针对性的解决问题,转子不对中故障的原因体现在这些方面:设计原因,如操作人员对热膨胀量的计算不够合理、未考虑到真空度、介质压力等对转子运作的影响,采用振动监测方式了解到,因转子材料质量不达标,导致运行环节其受热不均匀、相应的冷态数据达不到标准要求。重新定位并加固主减速机,将主减速机安置在不偏离中心线的位置上,利用钢板制作斜铁,及时调整好斜铁在底座的位置,从而确保中心线标高与主机之间的距离在设定范围内,避免位置偏差,防止设计阶段出现转子对中不平衡的问题。比如安装检修的环节,为保证故障诊断的有效性,及时校正并调整主减速机与三联箱中心线,最大限度控制好中心线误差,同时认真将存在污垢的三联箱清理干净,定期清洗并加润滑油,检修完成后还要利用水平仪检测两端法兰高标能够达到标准化操作要求。
摩擦故障振动监测诊断:旋转机械摩擦故障具有非线性的特征,当局部出现摩擦故障,频率成分较为丰富,当摩擦程度加重时,超谐波、次谐波等的阶次都减小,轴瓦磨损时,作业人员在分析润滑油样的环节发现磨粒沿着磁波线呈长链状排列。根据摩擦故障的特性,将振动监测技术灵活用于振动监测环节,针对旋转机械振动幅度、频率等,及时提出故障振动监测方法,同时考虑摩擦故障的处理过程,便于有序的展开摩擦故障处理,酌情增加润滑油的用量。
提高操作人员的专业技能:为防止旋转机械在运行中出现严重振动,作业人员平时要加强对旋转机械标准化操作及振动监测诊断等方面的知识,不断更新自身的知识结构,做好技术准备,以便在旋转机械出现振动故障时,能够运用专业知识进行振动监测,快速找到故障原因,并采用自学方式,强化专业知识吸收和巩固,使自身的能力更好的适应岗位工作。
结束语
综上所述:本文以旋转机械振动故障诊断为例,主要研究振动监测系统原理、旋转机械运行中常见故障、故障诊断振动监测系统设计、运用振动监测技术的关键、常见故障振动监测诊断及处理等内容。为促进振动监测技术有效运用,需加强振动监测系统的总体设计和软件设计,重视故障诊断,及时解决转子不平衡、转子不对中、摩擦故障等引发的振动问题,同时主动与专业有关的内容,注重振动监测技术在旋转机械故障诊断环节的利用,加强技术学习,从而提升专业水平。
参考文献
[1]侯长波,HouChangbo.转动设备振动在线监测与故障诊断技术的应用[J].冶金动力,2017(12):53-56.
[2]王江萍,段腾飞.旋转机械振动信号频域随机压缩与故障诊断[J].机械科学与技术,2018,37(2):293-299.
[3]吴飞,孟庆宇,吴振宇,等.旋转机械转子振动及噪声测量分析系统[J].数字制造科学,2018,v.16;No.69(02):10-14.
[4]张长森,赵秋实,吴君.基于Infogram的重复瞬态特征提取与旋转机械故障诊断[J].测控技术,2018,37(7):68-72.
[5]李德冲.基于改进型HILBERT--HUANG变换的旋转机械故障诊断系统设计[D].天津工业大学,2017.
[6]张峰,杨尚君,石现峰,等.旋转机械振动信号奇异值子空间分解滤波[J].西安工业大学学报,2017(8):634-640.
[7]郭信心,冯素菊,李想,等.应用LabVIEW的旋转机械振动监测系统的设计[J].山东工业技术,2017(16):7-8.
[8]商孝鹏.旋转机械设备振动监测诊断技术[J].冶金设备管理与维修,2017,35(5):20-25.
[9]何珊,梁红梅,蒋劲,等.小波分形算法在旋转机械振动信号特征提取中的应用[J].武汉大学学报(工学版),2017,50(1):129-136.
[10]于海祥,赵新杰,张龙.频率辅助信号结合EMD的旋转机械故障诊断[J].半导体光电,2017(2):271-277.
[11]蔡文方,陆颂元,吴文健,等.ICA在汽轮机组动静碰磨故障诊断中的应用研究[J].汽轮机技术,2017,59(6):451-455.
作者简介:屈海军(1980—),男,汉族,江苏徐州市人,硕士,江苏安全技术职业学院,讲师,研究方向:机械设计与自动化控制 机械设备维修