基于流固耦合的混流式水轮机转轮应力分析
日期: 2018/2/10 浏览: 2 来源: 学海网收集整理 作者: 江苏联合职业技术学院淮安生物工程分院 丁宁
摘要:混流式水轮机转轮在正常运行时,会因为水利因素导致转轮叶片发生疲劳断裂或者出现裂纹,为了让机组在合适的工况和频域区间运行,避免因为应力或是振动等问题发生叶片失效。本文基于流固耦合理论,采用顺序耦合法,通过建立转轮模型、CFD分析、流固耦合应力分析以及振型仿真等操作。分析额定工况和飞逸工况下的运行规律。
关键词:混流式水轮机;流固耦合;转轮应力;数值模拟分析
1 引言
本研究以某电站的混流式水轮发电机组为研究对象,进行流固耦合的应力性能分析。电站和机组的部分参数如表1所示。
表1 电站和机组参数

在对水轮机转轮的流固耦合的应力数值模拟分析过程中,由于应力分析的对象是转轮叶片实体,因此,最常用的建模方法是直接建立转轮实体模型,然后进行叶片强度计算。该方法具有操作步骤少、计算时间短等特点,但是计算精度的高低,却无法得到保证。由于转轮在水中运行,其承受的载荷有变化复杂的水压力载荷,以及与导水机构、尾水管等其余部件相互关联的力作用等,因而上述直接建立的转轮实体模型,只是一个单独的部件,在进行数值计算时,载荷的添加只能以表1中的最大水头值为基准,结合经验进行人工加载,这样显然与实际情况有所偏差,故无论是流固耦合的应力计算还是振型仿真,结果都不会十分准确。故建模方法需要进一步修正。
修正建模方案的目的,是为了改变传统建模方案中的载荷无法准确设置的问题,以达到提高计算精度的目的。而这一切的关键是能够提取与实际条件相一致的水压力参数,因此,在建立转轮实体模型之前,先建立一个全流道模型,并进行Computational Fluid Dynamics流场分析,便能够有效提出较为准确的水压力载荷参数,数值计算过程如图1所示。
综上所述,修正建模方案中,主要是多建立一个全流道模型,即需要完成全流道和转轮实体这两种模型的构建。
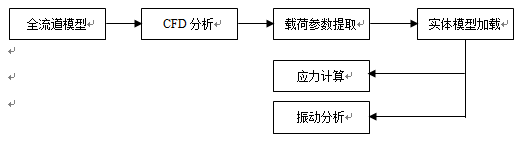
图1 数值计算流程
2 模型的建立
2.1 混流式水轮机全流道模型的构建
混流式水轮机全流道是指机组所有过流部件的内部流场。本文采用Catia三维造型软件来建立全流道模型,具体的操作步骤为:(1)分别建立蜗壳、导水机构、转轮、尾水管等过流部件的流场模型;(2)根据各部件流场之间的相对位置关系(例如:转轮中心线与尾水管进口中心线重合、蜗壳出口流面与固定导叶进口流面重合等),组合所有流场模型;(3)在三维软件中采用整体生成命令,将组合好的流程生成整体流场。全流道模型,如图2所示。
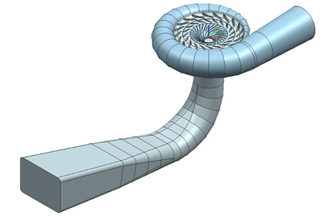
图2 水轮机全流道模型
2.2 转轮实体模型的构建
建立准确的转轮实体模型是有限元应力计算和振动分析的前提。转轮模型包括上冠、下环以及叶片3个部分,由于上冠和下环形状规则,故本文仅讨论短叶片模型的构建问题。
(1)叶片型线分析
混流式水轮机转轮叶片形状是光滑、复杂的,若将其结构抽象为面体,则包括:正面(雕塑曲面)、背面、进水边圆弧、出水边曲面等。叶片建模方法是将翼型在三维空间中以一定位置排列,将叶片投影到平面坐标轴上的轴界面,沿着Z轴,每隔相等间距,取样一个翼型截面,叶片翼型截面就包含有: 、 、 ……;绘制翼型时,建立截面的x,y坐标,沿y方向取若干等距离, , ,每一个 对应两个x坐标, 和 ,绘制出所有坐标点,将其连接成光滑的曲线,便完成了该截面翼型的绘制。在完成全部翼型的绘制和排列后,本文采用NURBS法,即通过样条曲线生成光滑的曲面。由于该曲线是通过NURBS拟合方程式来建立的,故相比于凭经验建模的传统方法,具有模型精度更高的优点。
(2)叶片曲面拟合
在Catia软件的实体造型模块,依照翼型截面的排列顺序,将已知的翼型曲线数据(.xls格式)逐个导入。通常情况下,三维造型软件中的样条曲线格式为NURBS,因此,在具体绘图操作中拟选择三次样条曲线。同时,虽然翼型数据是给定的,但是为了使叶片具有更高的光滑性,可以将叶片型线进行微调,使截面之间的过渡性更加良好。然后,采用“曲线组”命令,完成模型的曲面拟合。由于相邻翼型之间存在一定的距离,拟合后难免出现不光顺的情况(距离越远,不光滑的程度越高)。此时,选择“曲线光顺”对这些细节区域进行调整。再重复进行拟合操作,并通过观察法对模型进行判断,一直到模型质量满足要求,。
(3)叶片自由曲面的延展
以上构建的叶片模型,虽然给定了全部的翼型数据,但是绘制出的叶片模型却并不完整。原因在于 翼型之前的截面数据以及 截面之后的截面数据缺失;没有完成翼型的绘制,就无法进行曲面拟合。因此,完成整个叶片模型的构建,需要对未知数据区域进行曲面延伸。对此,本文采用样条曲线节点插入算法进行操作,具体介绍如下:
首先假设某条K次的NURBS曲线为已知,将各翼型坐标点导入Excel中,选择插入图表-散点图,完成曲线拟合,生成的方程式为

计算出新控制顶点后,将其投影至三维空间坐标,可得

由式(6)~式(8)可知,当新节点插入后,可以计算出NURBS曲线新控制顶点。
根据该方法,可以得到叶片未知区域的延展方法操作过程:
①利用上述算法,对转轮叶片的曲面边界曲线先进行离散化操作;其次,根据曲线对切向连续延伸的要求,对所有离散点所处的样条线展开延伸。
②将转轮上冠和下环的方程式,当作延伸的边界限制方程。同时,与延伸后的曲线拟合方程联立,计算出交点。依照该方法,将所有延伸的曲线都与上冠、下环的旋转曲面相交,由此获得到两组的交点,即为交线节点。
③将所有交点插值操作,生成NURBS曲线,如此可以绘制出叶片和上冠、下环的交线。
④最后,在三维软件中,采用“多截面实体”命令,生成未知区域的延展曲面,再将模型生成整体,完成叶片实体的构建,单个叶片模型,如图3所示。
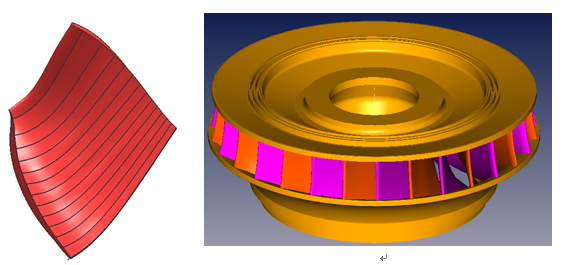
图3 完整叶片实体模型 图4 转轮实体模型
(4)光滑性检查
由于叶片模型的光滑性,直接影响到数值计算的精度。因此,对模型的光滑性质量检查,必不可少。本文采用平面检查法进行光滑性检测。由于在模型的建立中,对未知区域进行了延伸操作,所以模型的实际翼型数量要多于之前的给定值。因此,需要由已建立好的实体模型来生成新的翼型序列。
将新生成的翼型序列图按照一定角度,投影到平面坐标轴上。并在坐标轴上沿水平方向取平行线:AA、BB、CC、DD、...。由此可知,翼型截面与水平线存在交点。本文以第四个截面(即DD截面)为例进行说明。
首先,在三维软件中调入叶片实体模型;然后,以出水面为基准,绘制一个较薄的实体,该实体以转轮的中心为轴,并取间隔为 ,开始旋转命令,以切割叶片实体;最后,提取二者的交线,导入至二维绘图软件Auto CAD。观察该交线(DD交线)。通过检查可知,该截线比较光滑,切变化规律性很强,因此,该叶片实体模型的质量较高,可以用于后续的数值计算。
(5)采用同样的方法建立长叶片的光滑实体模型
(6)转轮整体模型的生成
在上冠、下环以及单个长、短叶片的实体模型构建完成后,将叶片模型环形阵列,生成转轮整体模型,如图4所示。
3 流固耦合的转轮强度分析
3.1 叶片应力数值计算
转轮强度的流固耦合分析,首先要进行的步骤,是对额定工况和飞逸工况下,机组全流道进行CFD分析,以便提取水压力参数。以额定工况为例,对全流道流场数值模拟中,选择湍流模型为标准 双方程模型,计算表达式为
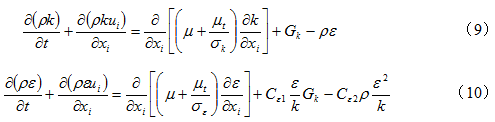
式中, 为湍流涡粘系数; 为湍流动能; 为湍流耗散率; 为平均速度梯度导致的 生成项; , 。
确定湍流模型后,在Ansys-CFD前处理步骤中,设置进口端为蜗壳速度进口,出口端为尾水管压力出口。选择标准 双方程模型,并按照第二章所述,设置计算方法为欧拉法,并确定流场控制方程等操作,迎风格式为2阶。最后,设置迭代次数为5000次,计算完成后,提取转轮叶片的水压力分布情况。然后在有限元强度性能分析时,做如下操作:(1)选择模型材料,结合以往同类型电站的叶片材料选取经验,拟初选材料为ZG00Cr16Ni5Mo,材料性能参数如表2所示;(2)提取水压力载荷数据;(3)在Ansys模块中,设置流固耦合命令,将水压力数据分别施加于每个对应叶片的正面和背面;(4)将额定工况和飞逸工况下的转速,加载于整个转轮;(5)上冠和主轴相关联的法兰面,设置全约束。
表2 材料性能参数
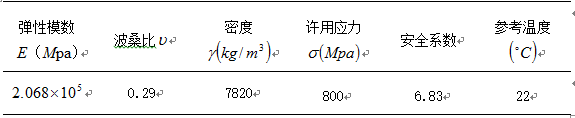
3.2数值计算结果分析
转轮叶片在运动过程中,承载的形式为水压力和离心力。因此,叶片上的应力分布主要是这两种力的综合作用。
(1)从CFD分析结果来看,转轮的进水边至出水边的压力逐渐降低,且叶片上的压降较小,故可知该转轮的水头损失较低,流态情况良好。
(2)额定工况下,上冠与下环的应力值基本均匀,且处于非常小的水平。相比之下,应力值较高的地方主要是叶片,且每个叶片上的应力分布并不是均匀的。但是总体而言,无论是叶片正面还是背面,压力都从进水边朝出水边方向减小。单个叶片承受的载荷水平并不高,长叶片的整体应力数值分布要高于短叶片的整体应力。进水边最大值位于长叶片与下环接近的区域,应力值仅为35.63Mpa,对应的最大位移量为0.22mm。由此可以得出:造成该处应力极大值的原因是叶片弯曲。在转轮叶片的出水边处,与下环接近的区域,存在整个转轮的极大值71.5Mpa,明显高于进水边的最大值。因此可知,在转轮旋转时,作用在叶片上的切应力要大于静应力。
从位移分布情况来看,叶片的位移变化趋势是沿上冠至下环逐渐增大。最大位移出现在下环附近。也就是说,叶片变形量最大的区域就在该位置附近。因此,在振动过程中,该位置属于敏感区域。
(3)飞逸工况下,上冠与下环的应力分布较之额定工况,变化规律更加明显。但是沿圆周方向,应力还是基本对称。从整体的应力水平来看,比额定工况要高。飞逸工况下的最大应力值区域与额定工况一样,出现在出水变长叶片与下环连接处,应力最大值为117.2Mpa。位移变化规律与额定工况相同,最大位移量为1.43mm。
表3 最大应力分布情况
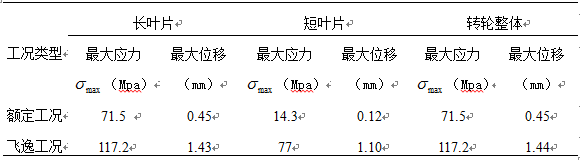
(4)由表1所示的ZG00Cr16Ni5Mo材料性能可知,该材料的许用应力值为800Mpa,安全系数为6.83。对比表3的数据可知,从强度性能来看,该转轮的力学特性是满足要求的。
3.3 应力试验
当转轮在额定工况和飞逸工况下的应力和位移分布情况模拟出来之后,为保证计算结果的准确性,需要对仿真结果进行试验验证。试验对象是针对该机组按比例缩小制作的玻璃钢材料模型,模型转轮直径为400mm。
(1)试验原理
由于试验是针对模型机组所有过流部件,测试参数类型较多。本文中仅选取单个模型长叶片正面应力值进行验证。试验的原理是:通过在叶片正面布置若干应变片,在应力加载的时候,材料会发生变形,应变片则会感应该测点的变形量,然后换算成应力值,并将结果传输置主机,最后将该模型应力值通过动力相似原理换算成真机应力,完成试验的测试过程。
试验操作流程为:(1)沿叶片的上冠至下环的流面出水边处,均匀布置4个应变片;(2)试验台的压力水箱按照与电站实际水头的比例调节高度,并使水流按照试验水头标准从模型蜗壳流入机组,从模型尾水管流出;(3)按照额定工况和飞逸工况的转速条件,使模型转轮达到相同转速;(4)开始测试,并采集数据,测试系统如图5所示。
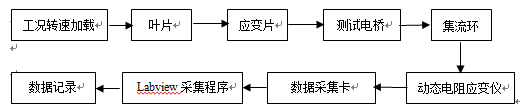
图5 测试系统流程图
(2)试验结果分析
通过对两种工况下,4个测点的数据采集,将试验结果与仿真值进行对比,如图6~图7所示。
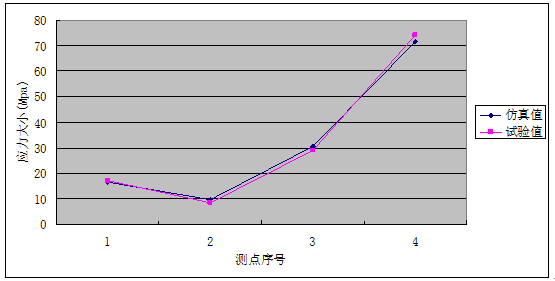
继续
图6 额定工况仿真与试验对比
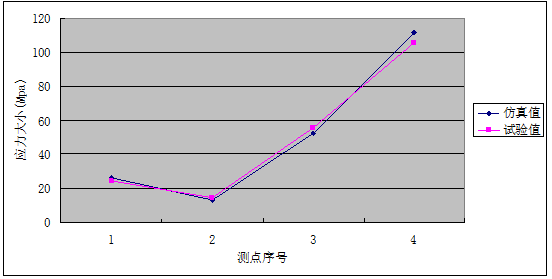
图7 飞逸工况仿真与试验对比
从两种工况下的试验结果来看,无论哪种工况下,4各测点的变化规律基本与仿真结果一致,额定工况下的最大应力为72.4Mpa,飞逸工况下的最大应力为112.6Mpa,与ZG00Cr16Ni5Mo的材料性能相比,同样是远低于其许用应力值,安全系数较高,故从静压方面来说,是不会造成叶片产生裂纹的。
对仿真结果进行验证,从试验和仿真值的对比可知,4个测点下二者的数值比较,误差也处于很小的水平,所有测点的平均误差约为 ,造成误差的原因在于:(1)转轮叶片形状的复杂性,转轮叶片是复杂非规则的光滑曲面,故实际中是无法达到理论上的设计精度的,故实际生产的模型和设计值有一定的偏差;(2)模型转轮属于焊接件,包括叶片与上冠和下环的焊接,由于转轮叶片较多,故焊缝也较多,因此焊接应力也会影响转轮的强度性能;(3)残余应力的影响,产品制造完成后,虽然有热处理的过程,但内部还有残余应力的存在。以上因素都是数值计算没有考虑在内的,故二者存在偏差。结合文献可知,该误差范围是符合要求的。
综上所述,该转轮叶片的强度性能较好,且有限元应力数值计算结果精度较高。
4 小结
本文主要是对基于流固耦合的混流式水轮机转轮应力分析。为提高计算的精度,分别建立了全流道流场模型和单个转轮实体模型。并采用NURBS曲线拟合对叶片主体造型,然后再用曲线节点插入法完成整个叶片实体模型的构建。最后,对转轮在额定工况和飞逸工况下,进行了流固耦合的强度分析和应力试验。计算结果表明,基于流固耦合的转轮应力特性分析,可以获取与实际运行条件接近的水压力载荷,计算精度较高,为后续的分析计算奠定了基础。
参考文献:
[1] 周东岳,祝宝山,上官永红,曹树良.基于流固耦合的混流式水轮机转轮应力特性分析[J].水力发电学报,2012(08).
[2] 肖若富,朱文若,杨魏,刘洁,王福军.基于双向流固耦合水轮机转轮应力特性分析[J].排灌机械工程学报,2013(10).
[3] 张新,郑源, 张德浩,王忠峰,尉青连.基于流固耦合的混流式水轮机转轮振动特性分析[J].水电站机电技术,2015(01).
[4] 孙琦,陈喜阳,章红雨,孙建平.基于流固耦合的水轮机转轮应力数值模拟分析[J].水电能源科学,2015(06).
[5] 石祥钟,赵文鲁,闫雪纯,刘安然.混流式水轮机转轮双向流固耦合力学特性研究[J].人民长江,2016(07).