模具设计中的工艺方案的确定
日期: 2019/2/10 浏览: 1 来源: 学海网收集整理 作者: 泰州技师学院 李荣林
[文章摘要]工艺方案的内容是确定冲裁件的工艺路线,主要包括确定工序数、工序组合和工序顺序的安排等,应在工艺分析的基础上制定几种可能的方案,再根据工件的批量、形状、尺寸等多方面的因素,全面考虑、综合分析,选取一个较为合理的冲裁方案。
[关键词]冲裁件 工艺路线 冲裁工序 模具制造
原始设计题目如下图所示:
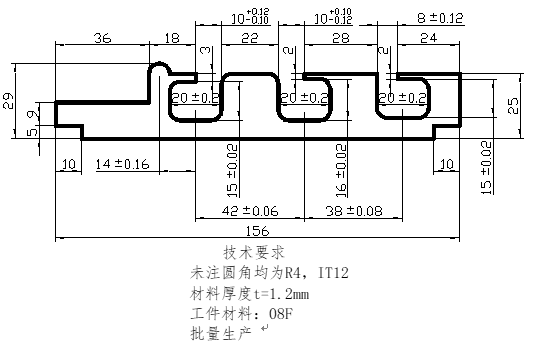
图1
冲裁工序的组合
冲裁工序按工序的组合程度可分为单工序冲裁、复合冲裁和级进冲裁。
复合冲裁是在压力机的一次行程中,在模具的同一位置同时完成两个或两个以上的工序;级进冲裁是把一个冲裁件的几个工序,排列成一定顺序,组成级进模,在压力机的一次行程中,在模具的不同位置同时完成两个或两个以上的工序,除最初几次冲程外,每次冲程都可以完成一个冲裁件。
冲裁组合方式的选择根据冲裁件的生产批量、尺寸精度、形状复杂程度、模具成本等多方面因素来考虑。
1. 生产批量
由于模具费用在制件成本种占很大的比例,所以,冲裁件的生产批量在很大程度上决定了冲裁工序的组合程度,即决定所用的模具结构。一般来说,新产品试制与小批量生产,模具制造简单,力求制造快,成本低,采用单工序冲裁,对于中批和大批量生产,模具结构力求完善,要求效率高、寿命长,采用复合冲裁或级进冲裁。
2. 冲裁件尺寸精度
复合冲裁所得工件公差等级高,内、外形同轴度一般可达到±0.02~±0.04mm,因为它避免了多次冲压的定位误差,并且在冲裁过程中可以进行压料,工件较平整,不翘曲。级进冲裁所得工件的尺寸公差等级较复合冲裁低,工件有拱弯、不够平整,但工序冲裁的工件精度较低。
3. 对工件尺寸、形状的适应性
复合冲裁可用于各种尺寸的工件。材料厚度一般在3mm以下,但工件上孔与孔之间和孔与边缘之间的距离不能过小。孔边距小于最小合理值时,若采用复合冲裁,则该部位的凸凹模的壁厚因小于最小极限值,易因强度不足而破裂。此时也不宜采用单工序冲裁,因孔边距过小,落料后冲孔时,这些部位会发生外胀和外扭变形,得到不合格的产品,这时宜采用级进冲裁,这样可避免这些缺陷。级进冲裁可以加工形状复杂、宽度很小的异形零件,且可冲裁的材料厚度比复合冲裁要大。但级进冲裁受压力机台面尺寸与工序数的限制,冲裁工件一般为中、小型件。为提高生产效率与材料利用率,常采用多排冲压。级进冲裁时广泛采用多排冲压,但复合冲裁则很少采用。
4. 模具制造、安装调整和成本
对复杂形状的工件,采用复合冲裁与采用连续冲裁相结合的方法,模具制造,安装调整较易,成本较低。对简单形状、精度不高的零件,级进冲裁,模具结构较之复合模简单,易于制造。
本次模具设计的冲裁工件形状虽然不规则,但结构并不是很复杂。冲孔、落料两道工序即可完成,考虑到冲裁件的定位误差、材料厚度、大批量生产、安装以及成本等因素,决定采用复合冲裁。在此有四种方案可供选择:
方案一:落料

图2 落料
此种方法的优点是:定位误差小,只需要一次定位即可,位置精度高。其缺点是:危险截面强度虽够,但模具制造复杂,难以加工和装配,并且成本比较高。
方案二:冲孔、落料

图3 冲孔、落料
采用落料、冲孔复合模。先冲孔,冲掉阴影部分,再落料。此种方法虽然降低了模具的加工和装配的难度,降低了制造成本。但是冲孔与落料的交界处留有尖角,难以加工和去除,这常常是冲压工艺所不允许的。
方案三:冲孔、落料

图4 落料、冲孔
也还是先冲掉阴影部分,再落料。此种方法虽然也和方案二有着同样的优点,此外比上述方案好的是冲孔与落料的交界处没有尖角,同时还能保证冲孔凸模和落料凹模的足够强度。
方案四:冲孔、落料
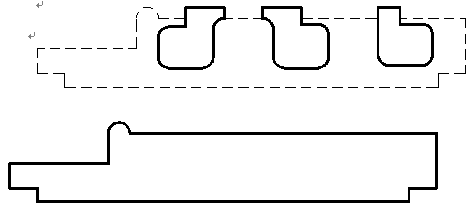
图5 冲孔、落料
此种方法是采取冲孔、落料分开加工两道工序,用两套模具。这样很容易产生定位误差,难以保证加工精度。
综合考虑上述四种方案,方案三还是比较理想的。在用一套模具能满足加工要求的前提下,尽量不用两套或多套模具来加工,所以,采用方案三为最终方案。
[参考文献]
[1]李名望主编,冲压工艺与模具设计 第2版,人民邮电出版社,2009
[2]张光荣主编,冲压工艺与模具设计 第1版,电子工业出版社,2009
[3]钟毓斌主编,冲压工艺与模具设计 第2版,机械工业出版社,2009