充气柜生产线工序重组与平衡研究
(常州博瑞电力自动化设备有限公司,江苏 常州 213000)
摘要:以某企业充气柜装配、焊接及试验产线生产过程为研究对象,践行精益生产理念,运用工业工程技术和生产线平衡等方法对产线进行分析,优化工序资源,设计专用工装器具,促进员工作业标准化,减少非增值活动,提高生产线平衡率,提升企业综合竞争力。
关键词:工序重组;生产线平衡;标准化作业;非增值活动
问题的提出
国家电网提出《配电设备一二次融合技术方案》与智能电网建设,旨在提升供电一二次装备的标准化、集成化程度,健全一二次装备联调的体系与标准,提高配电装备的运维质量。实现一二次设备融合面临诸多问题,特别对电力设备生产行业提出的高要求,需要生产厂商在技术与设计方面加强投资,采用自动化程度高的先进设备,持续提升产品质量[1]。
充气柜作为交流配电网系统核心产品,是电力工业中重要输配电设备,其生产过程需要将负荷开关、断路器、铜排、套管等主要元件安装在半封闭的气箱内,并对气箱后封板进行焊接固定,在装配过程中需穿插机械磨合、机械特性、充气检漏、耐压局放等测试。产线生产存在工序多、工位间多次穿插、工序节拍不一致、生产线平衡率低、员工生产效率低等问题。为进一步降低产品制造成本,提高产能及产品质量,针对生产线运用工业工程技术,通过工序作业价值流分析,实现量产产品的作业标准化、节拍最优化,落实工序重组,降低劳动强度,为生产线均衡化提供依据,最终达到充气柜生产线平衡优化的目的[2]。
生产现状分析
现有充气柜生产线主要用于主器件装配、机械磨合测试、机械特性测试、回路电阻测试、气箱封闭焊接、充气检漏、耐压局放测试、柜体合装等工序的自动化生产,通过运用RGV穿梭车自动控制及激光测距定位技术,实现工件在各工位间的自动化流转。该生产线各工序布局如图1所示,共有15道工序,17人,每天产出8台,客户对此产品需求大约为每天10台。整条产线人员工作强度参差不齐,存在较多非增值活动。
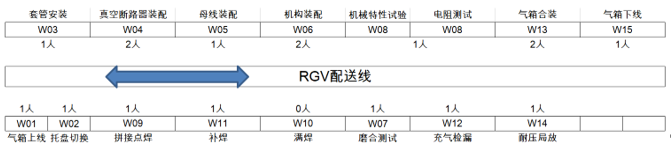
图1 优化前各工序布局图
对各工序采用多次秒表测时法[3],获得优化前的作业时间见表1。
表1 优化前各工序作业时间
工序编号 工序名称 作业时间(min) 作业人数
01 工件上线 15 1
02 托盘切换 30 1
03 套管装配 45.5 1
04 真空断路器装配 46 2
05 母线装配 19.6 1
06 机构装配 25 2
07 磨合测试 32.8 1
08 机械特性试验/电阻测试 27.8 1
09 拼接点焊 38 1
10 自动满焊 27 0
11 补焊 56.5 1
12 充气检漏 35 1
13 气箱合装 27 2
14 耐压局放 53 1
15 工件下线 32 1
多次观测得出补焊工序是瓶颈工位,平均节拍时间(CT)是56.5min。各工位员工每天工作7.5小时,可计算出理想状况下:
理论日产能=7.5×60/56.5=8<10(台)
产线的生产能力不满足客户需求,急需提高。
计算得出满足需求的生产线节拍=450/10=45min。图2为各工序作业时间与需求节拍对比,可直观看出各工序与需求节拍的差距。
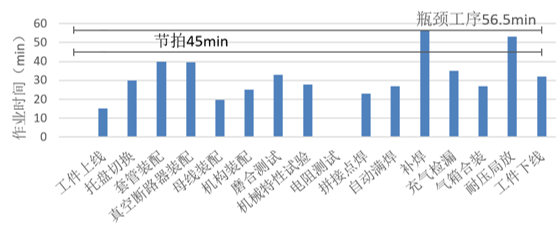
图2 各工序作业时间与需求节拍对比
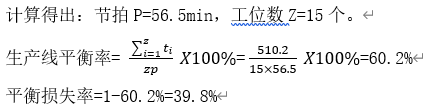
可以看出各工序作业时间与节拍差距较大,瓶颈工序补焊制约着整条产线的效率,导致生产线平生损失率39.8%。
采用鱼骨图[4]把整个系统分解成人、机、料、法、环五个要素,梳理整个系统的问题,具体如图3。
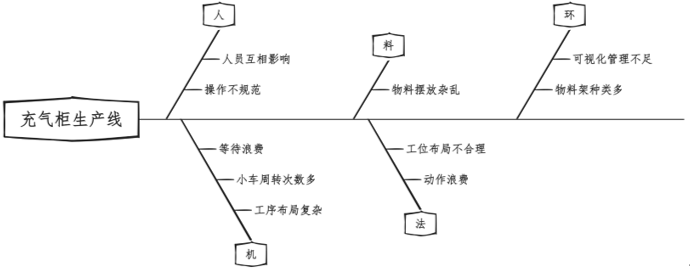
图3 充气柜生产线鱼骨图
对生产线分析优化
3.1工装器具改进
开发气箱定位工装,以气箱折板及侧板为定位基准,使气箱摆放位置与产线工位固定位置保持一致,确保气箱与滑撬准确快速安装,避免气箱二次翻转,减少非增值活动。
优化套管装配工序,设计套管专用物料架,配置防护隔套,解决原先人员弯腰取放安装过程中易碰撞划伤等问题,提升人员近手化作业水平。
设计真空断路器、机构物料工装车,按照一备一用原则进行物料配送,减少重复搬运浪费。
统一工位工具车,工具、辅料、工艺文件要求标准化摆放,杜绝人员工具随意摆放、辅料频繁缺失、工艺文件不识别等违规操作。
改进线束测试工装,实现公母头接口对插,减少耐压局放工位试验接线准备时间。
3.2工序重组与人员配置调整
取消托盘切换工序,托盘切换工位与气箱上线工位靠近,设计气箱定位工装后,气箱上线时间仅需要7分钟,人员工作强度相对较小,与托盘切换工序合并由1人完成。
取消母线装配工序,与磨合测试工序合并。母线装配工序节拍为19.6min,磨合测试工序人员准备时间仅8min、设备运行时间25min,新增一台磨合设备同步试验,两工序合并后节拍为40min左右,减少1名人员投入。
取消下线工序,将气箱合装工序与下线工序合并,由气箱合装工序人员完成下线工序收尾工作,减少1名人员投入。
补焊工序增加1名作业人员,2人共同完成补焊工作,加快节拍。
3.3关键工序作业标准化
套管装配工序,物料、工具等定置定位,便于员工精准获取,提高效率;明确套管放置方向、紧固螺钉型号数量,防止质量问题;细化套管压板装配步骤及要求,明确工具型号、紧固顺序、划力矩线、检查卡填写等要求。确保员工作业标准化,减少动作浪费。
真空断路器装配工序,细化作业流程,制定断路器摆放要求,规定机械臂抓取位置,固化机械臂运动轨迹。解决原作业方式抓取工件位置不定、安装孔位找正困难、操作节拍不稳定等问题。
3.4管理看板应用
制定生产节拍目标,分解阶段性计划,展示计划达成情况。
展示产线工位组织架构,明确责任人及职责。
展示产线布局图,规划作业区域、物料区域、产品移动区域等,便于现场6S管理。
展示人员技能矩阵图和技能培训计划,针对性提高员工技能。
生产状态目视化改善,根据日订单确定每台产品计划下线时间,记录下线时间,对于异常下线复盘后制定改善措施。
展示改善项目清单,根据课题清单进行攻关技改。
优化效果评价
根据以上优化方案进行产线平衡后,整条线工序数由15个减少到12个,人员由17人减少到14人。优化后各工序作业时间见表2。各工序作业时间对比见图4,优化后生产线各工序安排更合理,具体见图5。
表2 优化后各工序作业时间
工序编号 工序名称 作业时间(min) 作业人数
01 工件上线/托盘切换 31.2 1
02 套管装配 33.2 1
03 真空断路器装配 30.1 2
04 机构装配 31.8 1
05 母线装配/磨合测试 36.8 1
06 机械特性试验/电阻测试 27.8 1
07 拼接点焊 28.6 1
08 满焊 27 0
09 补焊 37.8 2
10 充气检漏 27.5 1
11 气箱合装/下线 37.2 2
12 局放耐压 35 1
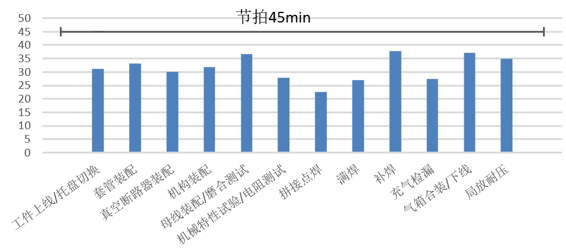
图4 优化后各工序作业时间对比

图5 优化后生产线布局图
节拍P=37.8min,工位数Z=12个
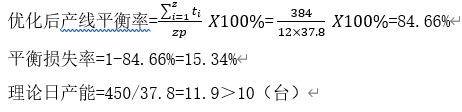
根据表3可以看出,优化后人员与工序数量均减少,消除了生产过程的等待浪费、搬运浪费、不良品浪费、动作浪费;生产节拍大大加快,同时提高生产效率和质量,满足了客户订单需求。
表3 优化前后数据对比
对比项 人数 工序数 生产节拍(min) 平衡率(%) 理论产量(台)
优化前 17 15 56.5 60.2 8
优化后 14 12 37.8 84.65 11.9
结论
工业工程中的生产线平衡是消除生产线中不必要的浪费,提高生产线效率、减少人员投入,降低生产成本。本文运用工业工程技术和生产线平衡等方法对产线进行分析[5],通过重组优化工序,减少各类过程浪费;制作专用工装器具,实施标准化作业,落实管理看板应用,推进车间6s管理等。减少产线人员投入,减低人力成本,提高产线平衡率,增加产能。通过生产线工序重组与平衡,充气柜生产线的生产能力不足问题得到解决。
参考文献
[1]黄伦,张欣宜,冯思朦.智能一二次融合柱上开关高可靠性关键技术研究[J].电子设计工程,2021,29(20):115-118+128.DOI:10.14022/j.issn1674-6236.2021.20.024.
[2]樊迅,阚树林,边潇.电抗器装配生产线的作业分析与平衡研究[J].机械制造,2011,49(01):83-86.
[3]徐从武.基于秒表测时法的工时定额制定[J].农业装备与车辆工程,2018,56(06):97-100.
[4]顾萍萍,杜敏.基础IE在生产线平衡中的应用研究[J].物流科技,2013,36(10):100-102+129.
[5]吴雪冰,温艳.企业生产线平衡分析研究[J].物流科技,2017,40(12):31-35.DOI:10.13714/j.cnki.1002-3100.2017.12.008.