在普通车床上车磨等分球窝的夹具及主轴设计
日期: 2020/3/21 浏览: 4 来源: 学海网收集整理 作者: 学海网
【摘要】对于加工圆周分布的球窝,没有适合的通用或专用设备。研究对普通车床改造,实现车磨两用加工等分球窝。对刀架进行改造,装上小拖板,正常车球窝;去掉小拖板,换上安装在中托板上的砂轮主轴,以磨球窝。设计了安装在车床主轴上的可分度的专用夹具,实现一次装夹多工位加工。提出了刀架改造方案,设计相应的磨削装置电主轴,对高速电主轴的支承、冷却、润滑、密封、预紧等进行了设计分析和研究。
关键词:机床改造;车磨两用;分度;夹具;电主轴
Key word:
中图分类号: TG502,TG75 文献标识码:A
引言
对普通机床进行改造代替购置专用机床,以完成专项产品的加工或提高加工效率,既便捷又经济。在单件小批生产中,选用现有的通用设备,经过适当改造,来完成特殊产品的加工任务,是企业的首选。
图1是要加工的零件球面凹模,其端面上等分均布着n个球半径为SR、深度为h的球窝。该球窝球半径、深度的尺寸精度为H6,表面粗糙度为Ra0.4,需要经过粗加工、磨削、研磨才能保证要求。该零件的品种规格多,批量小,n、SR、h各不相等,应首先考虑在普通机床上加工。拟在普通车床如CA6140上完成球窝的车磨加工。
图1 球面凹模
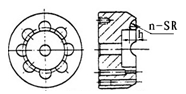
1 设计思想
1.1内球面加工方法及成形原理
内球面加工常用的方法有成形法、轨迹法和展成法。用成形车刀车、成形锪钻钻等属于成形法;用圆柱砂轮、工件摇摆的摆头磨属于轨迹法;用圆柱立铣刀铣、圆柱砂轮磨等属于展成法。本设计中,球窝属于内球面,车球窝用成形法,磨球窝用展成法。
展成法磨削内球面的成形原理如图2所示,砂轮轴线相对于工件轴线偏转α角,两者相交于O点。砂轮端面和球半径为SR的球面相截,所得的截形始终是一个偏心距为e、直径为砂轮直径d的圆。当砂轮和工件绕各自的轴线旋转时,这个偏心距为e、直径为d的圆绕工件的轴线旋转形成了内球面。砂轮轴线的偏转角α可以用下式计算:
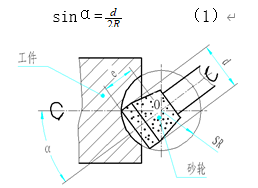
图2 内球面磨削原理
1.2 改造总体思路
设计安装在车床主轴上的专用夹具,使夹具中心相对于车床主轴的中心偏移一个球窝的中心半径,将一个球窝的中心置于车床主轴的中心,进行车或磨加工;再通过分度机构,将圆周分布球窝的中心依次置于车床主轴的中心,实现一次装夹多工位加工。粗加工时,刀架不变,用成形车刀车球窝;精加工时,去掉刀架上的小拖板,换上安装在中托板上的砂轮主轴,将砂轮主轴座旋转,使砂轮主轴轴线相对于车床主轴轴线倾斜一定角度,用圆柱砂轮磨球窝。同样可以用改造后的车床磨圆周分布的直孔,方法是砂轮主轴座不旋转角度,即砂轮主轴轴线平行于车床主轴轴线。
2 设计内容
2.1专用夹具的设计
专用夹具结构如图3,夹具安装和卡盘的安装类似,通过夹具体1左端面和内锥孔在机床主轴定位,用四个螺栓固定在主轴上。
夹具体1上有定位槽,槽内装有滑块3,用滑块移动来调整偏心距,使球窝中心和主轴中心重合。滑块上有圆柱面和分度盘4的定位孔配合,另一端有方形定位键4与分度盘的等分槽单面靠紧定位。为了使相同等分的工件可以使用同一个分度盘,在分度盘上装有过渡盘5,通过螺钉与分度盘固定成一体,并用压板固定在夹具体上。工件通过环型压圈8固定在过渡盘6上。夹具体上方有一个配重块2,用来平衡偏心夹具旋转产生的不平衡力。
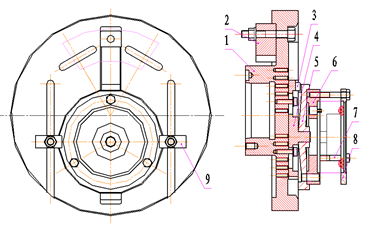
图3 车球窝等分夹具结构图
2.2 刀架改造
2.2.1 总体设计方案
刀架改造的要求是在刀架上增加一套磨削装置,其主要部件是砂轮主轴。因为球窝直径不大,为了保证磨削质量,砂轮线速度要达到20~32m/s。因此在砂轮主轴的结构摒弃了传统的齿轮和皮带传动,采用高速电主轴作为动力源。
本设计方案是把普通车床刀架上的小拖板去掉,安装上磨削装置。磨削装置包括电主轴支座、支座座板,电主轴,以及配套的改变电主轴转速的变频器等。支座底面到主轴中心的高度应实际测绘,以保证砂轮主轴和车床主轴的轴线等高。电主轴安装示意图如图4所示,支座座板2下面的凸圆柱以小间隙配合(H7/H6)装在中拖板1的定位孔中,支座座板可相对于中拖板任意旋转,按公式(1)计算出的偏转角α旋转后,用原来用来夹紧小拖板的两个T型螺钉5夹紧。支座座板2通过两个定位销7和四个螺钉与支座3连成一体,电主轴2通过压紧螺钉6固定在支座座孔中。
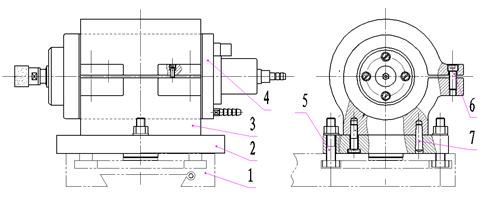
1中拖板 2支座座板 3支座 4电主轴 5 T型螺钉 6压紧螺钉 7定位销
图4 电主轴安装示意图
2.2.2电主轴的结构设计
电主轴性能的好坏在很大程度上决定了整台机床的加工精度和生产效率。电主轴的主要工作原理是直接将空心的电动机转子6热压在主轴2上,定子7固定在主轴壳体5孔内,形成完整的主轴单元。通电后直接带动主轴运转,进行磨削,省去了带轮或齿轮传动。本研究开发的高速磨削电主轴,结构上采用当前比较流行的内置电机、水循环冷却、角接触混合陶瓷球轴承支承、油雾润滑及定压预紧的典型型式。
图5是电主轴结构示意图。件5是轴壳,用来支承旋转件并安装到支座上。件1为砂轮接头,其主要作用是连接砂轮到主轴2上。 最左端的防尘盖件2为保护件,防止灰尘、进入轴承内部。因为电主轴轴承为高精密件,灰尘的进入会影响轴承的寿命。主轴前支承是一对串联的角接触混合陶瓷球轴承件4。后大盖8右端有均匀分布的弹簧,使后轴承11的外圈始终受到一个向右的推力作用,使前后轴承产生预紧力。滚珠导套10的作用是提高后支承的支承刚度,同时又减小后轴承预紧或热伸长时后移的阻力。轴承件12为平衡块,通过在其上钻孔使主轴2达到动平衡,保证其旋转精度。件6和件7是转子和定子,其主要是形成轴的转动。件13是定子防水套,其主要作用是防止水进入定子,引起短路。件11和 件14分别为油管和水管接头,其主要作用是连接油管和水管。
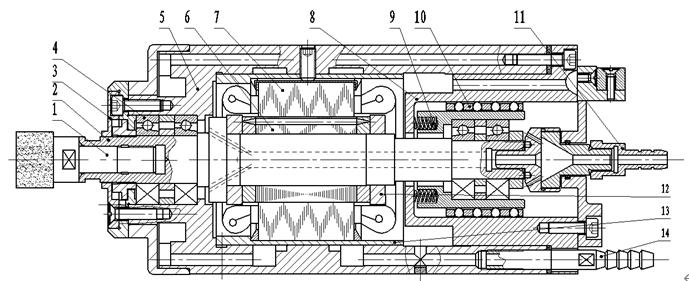
图5 电主轴结构示意图
2.2.3电主轴设计的关键技术
设计的电主轴的极限转速为36000r/min,精度为主轴左端的轴向跳动和径向跳动不超过0.003mm。
电主轴设计的关键技术包括支承方式、预紧、冷却、润滑,动平衡技术等。
(1)支承技术 主轴支承方式上采用前后两支承,各采用两套串联的角接触球轴承,前后支承之间形成背靠背,这种支承方式延长了实际的支撑跨距,可以减少砂轮的实际悬伸长度从而减小受力变形。这种支承方式比较适合高速主轴。本设计采用了角接触混合陶瓷球轴承 ,混合陶瓷球轴承采用陶瓷滚珠材料,具有高刚度、低温升和长寿命的特点,是高速主轴的发展方向。
为了保证主轴的旋转精度,主轴前端轴承选用P2级精度,后端选用P4级精度。轴承选配后,采用误差抵消调整法装配,可提高主轴的装配精度。
(2)冷却 对于高速旋转的主轴,轴承和内置电机是两大热源。在电主轴工作时,发热使主轴的局部温升过高,轴的热变形加大,影响加工精度。本设计采用了外循环水冷却系统。电主轴工作时,水管接头接冷却水,由水管进入冷却系统,对轴承、定子和转子进行循环冷却。
(3)润滑 润滑可以有效减少轴承运转时的发热。选用油雾润滑方式,利用压缩空气将油雾化,再经喷嘴喷射到所润滑表面。由于压缩空气和油雾一起被送到润滑部位,有较好的润滑作用。图6右端油管接头11是油雾的进口,在2~3个大气压的压力下从中空的主轴内部通过,分别对前后端轴承进行润滑,然后从壳体侧孔流出,同时起到一定的散热作用。
(4)预紧 合适的预紧可以增加轴承的刚度,提高旋转精度,降低振动噪声,延长使用寿命。本设计采用定压预紧,这种预紧方式可以使主轴获得稳定的径、轴向刚度。
(5)动平衡技术 由于高速电主轴的转速很高,因此即使微小的动不平衡量,也会产生很大的离心力,引发振动。对于电主轴的主轴组件动平衡要求,取ISO标准G0.4 级。
结论
通过设计安装在车床主轴上的专用夹具和安装在中托板上的砂轮主轴,按本方法对普通车床改造,可以实现车磨两用加工等分球窝。实际应用表明,该方案切实可行。本文所说的方法,在产品批量不大、购置专用机床不经济的情况下,对企业具有参考意义。
参考文献
[1] 孟少农.机械加工工艺手册.北京.机械工业出版社.1992.
[2] 夏广岚,冯凭.金属切削机床.北京大学出版社.2008.
[3] 贾群义.滚动轴承的设计原理与应用技术.西北工业大学出版社.1991.
[4] 赵雪松,赵晓芬.机械制造技术基础.华中科技大学出版社 .2006.
[5] 张伯霖,夏红梅,黄晓明. 高速电主轴设计制造中若干问题的探讨. 制造技术与机床.2001
[6] 李鹏,张中元,郝玉萍等.多联角接触球轴承组配中预载荷和变形的分析.轴承.2003
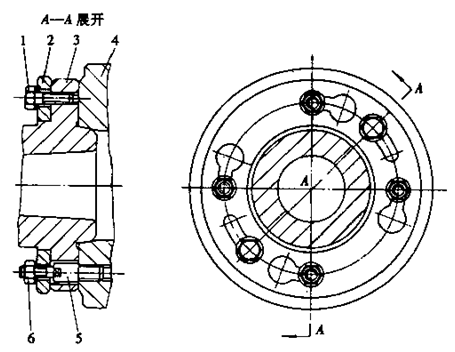
1一螺钉 2一锁紧盘 3一主轴 4一卡盘座 5一螺栓 6一螺母
图2-6 CA6140卧式车床主轴前端短锥法兰式结构