数控车加工尺寸的控制技巧
摘要:机械加工的最终目的是保证尺寸精度与表面粗糙度,在现代制造业发达的今天,数控车削加工技术已广泛应用于机械制造行业,数控车床上加工零件的尺寸精度要求是比较高的,,如何利用数控车床高效、合理、按质按量完成工件的加工就显得尤为重要。
关键词:加工尺寸;尺寸中值;刀具磨损偏置;控制技巧
一、引言
数控加工刀具运动的轨迹是由程序控制的,如果编制程序时合理选择切削用量,那么表面粗糙度基本上是可以达到要求的,但由于刀具磨损、对刀误差等因素会造成加工尺寸的误差,所以要想达到图纸上的尺寸精度要求,首先要仔细看图纸并能编制正确的程序,其次要找到图纸中的关键尺寸及其公差,制定尺寸控制的方法。
二、加工尺寸的控制技巧
1.编制程序保证尺寸精度
1)运用绝对坐标编程保证尺寸精度
编程有绝对坐标编程和增量坐标编程。增量坐标是指起始位置到目标点的移动增量,也就是说,增量坐标编程的坐标原点经常在变换,连续位移时必然产生累积误差,而绝对坐标编程在加工的全过程中,只有一个坐标原点,所以累积误差没有增量坐标编程大。数控车削工件时,工件径向尺寸的精度一般比轴向尺寸精度高,所以在编写程序时,径向尺寸最好采用绝对坐标编程,有时考虑到加工及编写程序的方便,轴向尺寸常采用增量坐标编程,但对于重要的轴向尺寸,最好采用绝对坐标编程。
2)取极限尺寸的平均值作为编程尺寸
为偏于控制零件轮廓尺寸的精度要求,编程时常取极限尺寸的平均值(尺寸中值)作为编程尺寸。
如图1为加工件示意图,其加工工艺为:车左端面、粗车左轮廓、精车做轮廓、掉头、车右端面、粗车右轮廓、精车右轮廓、车退刀、车螺纹。车左端时,工件坐标系取在左端面,加工余量为2mm,拟采用粗、精车,应用复合固定循环指令G71、G70指令编程。图中直径尺寸有公差要求,且公差不等,为此在编写程序时将其换算为公差带对称分布的尺寸。
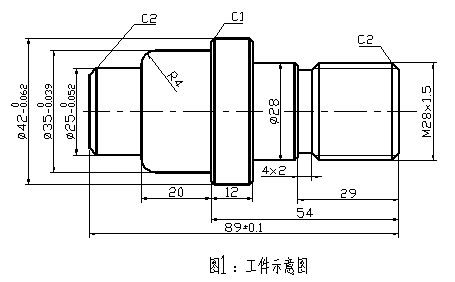
参考加工程序如下:
O0001;
T0101;
M3 S600;
G00 X47 Z5 ;
G71 U2 R1;
G71 P10 Q20 U0.5 W0.1 F0.25;
N10 G01 X20.974 Z0 F0.1;
X24.974 Z-2;
Z-15;
X26.981;
G03 X34.981 Z-19 R4;
G01 Z-35;
X39.969;
X41.969 Z-36;
Z-48;
N20 X47;
G00 X100 Z50 M5 ;
N30 M0;
T0202;
M3 S800;
G00 X47 Z5;
G70 P10 Q20;
G00 X100 Z50 M5;
M30;
2.选择公差最小的尺寸作为监控尺寸,加工时通过调整磨损偏置控制该尺寸。
FANUC系统中刀具指令为T后跟四位数字组成,前两位为刀具号,后两位为刀具补偿号,同一个刀具号可以调用不同的刀具补偿号,这就为刀具指令控制尺寸提供了更多的选择。FANUC系统将刀具偏置分为两部分,一是刀具外形偏置,二是磨损偏置,使用刀具磨损偏置可以微调刀具位置从而达到控制加工尺寸的目的。
图1左侧,公差最小的尺寸是¢35 0 -0.039(¢34.981+ -0.02),可以以此作为监控尺寸,若该尺寸合格,其余尺寸公差更大的尺寸自然合格。
当程序运行到N20程序段时,停车测量精加工余量。根据精加工余量设置精加工刀具(T02号)磨损量,避免因对刀不精确而使精加工余量不足而出现缺陷。然后运行精加工程序,程序运行到N30时,停车测量;根据测量结果,修调精加工车刀磨损值,再次运行精加工程序,直至达到尺寸要求为止。
图1左侧程序可以将T02号刀具X磨损量设为0.3mm,Z磨损量设为0.2mm。精加工程序运行后,测得¢35 0 -0.039mm外圆实际尺寸为¢35.2mm,比平均尺寸大0.221mm,单边大0.111mm, 根据“大减小,小加大”的原则,则把X方向磨损量修改为0.3-0.111=0.189mm。修改刀具磨损量后,重新运行精加工程序,直至达到尺寸要求。
长度尺寸在停车测量时可以通过修改Z方向的磨损量来控制尺寸。
数控车床上首件加工均采用试切和试测方法保证尺寸精度,首件加工尺寸调好后,将程序中M0M5指令删除即可进行成批零件的生产,加工中不要再测量和控制尺寸,直至刀具磨损为止。
三、结束语
数控车削加工是基于数控程序的自动化加工方式,实际加工中,操作者只有具备较强的程序指令运用能力和丰富的实践技能,方能编制出高质量的加工程序,加工出高质量的工件。