12Cr1MoV耐热钢管的焊接工艺
日期: 2021/1/10 浏览: 0 来源: 学海网收集整理 作者: 南通职业大学技师学院 王斌
摘要: 本文对12Cr1MoV钢管的焊接工艺做了详细的介绍,并就焊接过程中遇到的焊接冷裂纹、再热裂纹、气孔等问题进行了分析,并从操作技巧的角度总结了一些避免缺陷的措施,大大的提升了焊接质量。
关键词:12Cr1MoV 珠光体耐热钢 冷裂纹 气孔
一、前言
南通某热电企业检修中锅炉小溢流管改造工程中,涉及到12Cr1MoV管的焊接问题。由于位置特殊,该耐热钢要承受高温高压、腐蚀、应力等因素影响,所以焊接质量的好坏决定了设备的使用寿命。好的焊接技术、合理的焊接工艺,严格的工艺保证措施是保证焊接成功的关键。下面就12Cr1MoV耐热钢,φ365×30mm管道焊接为例,将在检修项目工作中研讨的12Cr1MoV耐热钢的焊接工艺措施与质量保证措施做详细的介绍。
二、12Cr1MoV珠光体耐热钢介绍:
1、12Cr1MoV珠光体耐热钢特性:
12Cr1MoV耐热钢是铁素体和渗碳体组成的机械混和物。而珠光体耐热钢在室温时的金相组织基本为珠光体加铁素体。由于这类钢是在碳素钢的基础上增加一定含量的合金元素,在高温下不但具有高的耐热性,而且热强性也较高,工艺性好,比较经济,应用广泛。
2、12Cr1MoV材料的化学成分与机械性能,见表1和表2:
表1 12Cr1MoV材料的化学成分%

表2 12Cr1MoV材料的机械性能
REL(Mpa) RM(Mpa) A (%) AKV(J)
≥255 470—640 ≥21 ≥40
3、12Cr1MoV钢材的焊接性
12Cr1MoV珠光体耐热钢,合金总含量较高,碳含量为0.12%,由于淬硬倾向大,易产生冷裂纹(多出现在焊缝和热影响区),焊后热处理时容易产生再热裂纹,因此厚壁大径管焊接时常需要焊前进行预热,焊接过程中要控制层间温度,焊后还要进行热处理。
三、12Cr1MoV钢,φ365×30mm对接接头氩电联焊焊接工艺
1、焊前准备
①坡口:用坡口机开U型坡口,见图1。坡口尺寸为α=10°~15°、b=2~3mm、p=1.5~2mm、R=5mm 。清除坡口及焊缝两侧10~15mm的油锈污物直至发出金属光泽。
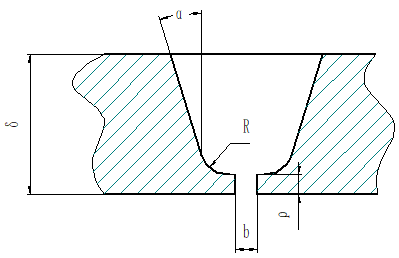
图1 坡口图
②焊机:准备逆变焊机两台。钨极氩弧焊和焊条电弧焊工具各一套。
③焊材:选择焊材时应注意其化学成分和力学性能、工艺性能等,这是获得优良的焊缝金属成分、组织和力学性能的前提。经过比较,我们确定焊丝选用TIG-R31,φ2.5mm,焊条选用R317,φ3.2mm和φ4.0mm两种规格。焊条严格按规定烘干后,装入保温筒内随取随用。氩气的纯度不低于99.99%。
④焊接预热:由于12Cr1MoV规格为φ365×30mm,管径大,壁厚大,最好采用电加热法预热。但一般的单位电加热的条件不易达到,多采用氧-乙炔加热法。用氧-乙炔加热,升温慢,劳动强度大,加热温度也不均匀,温度不易控制,如果要使用必须注意加热部位的温差不可过大。 预热200-300℃,预热长度不得低于60mm。
⑤其他要求:持有相应合格焊工证书的焊接人员两人,热处理人员必须经过专业培训并考核取得资格证书。焊接场所的环境应维持在-10℃以上。不得强制对口,应用管夹对接,不得在焊缝直接点焊对接。
2、焊接操作过程
①氩弧焊打低:打底时管子内不准有穿膛风,打底焊层厚度不应太薄,应不低于3mm。最好使用内填丝法进行焊接。
②焊条电弧焊填充盖面:打完底层后,立即进行第二层电弧焊的焊接,焊条应用φ3.2mm,焊接电流不应太大,以免第一层被烧穿,两人必须同时施焊。当焊完第二层时必须将飞溅、夹渣、药皮等杂质清理干净,因为焊条是低氢型,产生气孔的可能性比较大,尽量采取短弧焊接,焊道的单层厚度不应大于所用焊条直径加2mm,单道摆动宽度不应大于所用焊条直径的5倍,收弧时应将熔池填满,焊层和焊道之间的接头应错开,除第二层用φ3.2mm焊条外,其余焊层均应采用φ4mm的焊条施焊。
③保证焊接过程层间温度不低于预热温度的最低限即200℃,且不高于400℃。
四、操作过程中容易产生的缺陷极其防止措施
1、冷裂纹产生原因
裂纹中尤以最为常见,大多产生于起头和收弧处,收弧裂纹最多,热影响区冷裂纹最少。针对上述情况,本人认为:起头(或称起弧)裂纹和热影响区裂纹主要是预热温度不够,不均和施焊中没有始终保持好整个焊件的温度,或者中间间断所致,同时施焊方法有问题。
2、冷裂纹防止措施
①确保正确的预热温度。无论氩弧打底还是手工电焊打底引弧后切不可急于填充焊丝(条),而应给予一定的电弧预热时间,当看到两边的钝边达到融化状态时,再填加焊丝(条),注意电焊时不准拉长电弧预热。同时,打底层不可太薄,尤其起弧处更不可太薄,增加它的厚度以减缓他的降温速度来达到避免冷裂纹的产生。注意上述问题,起头(其弧)处和热影响区的裂纹一般均可避免。
②用回焊、慢熄弧的办法解决弧坑裂纹问题。收弧处(弧坑)裂纹的形成,就是因为冷却速度过快而造成的。回焊法一般指手动电弧焊而言,就是在收弧时已将弧坑添满了,不需要急于迅速停焊,而是应以短弧断续焊的方法再回过来点几下,一般三点便可,注意最后一点应点在熔池的边缘为宜,以此方法来转移熔池的最高温度点(熔池中心)和缓解冷却速度,达到避免裂纹的产生。同样,氩弧焊收弧时也应加几点焊丝并将熔池最高温度点向边沿转移,并逐渐拉长电弧慢慢地熄弧。
3、气孔的产生原因
气体的来源有①焊件清理不干净②环境或者保护不力,如风过大,有穿膛风,焊枪角度不对等。③氩气不纯。④母材和焊材本身产生的氢气体。氢气孔的形成是由于氢气体没有及时逸出熔池金属而形成的。造成没有及时逸出熔池的原因有两个:在不停弧的情况下一是由于金属的结晶是逐渐有柱状形成,而柱状晶体最早产生点是在两边坡口先形成,相对方向快速长大并逐渐交叉在一起和熔池根部的晶体一同形成焊缝金属(固体)当两边的柱状晶体交叉在一起的速度快于气体外逸速度时,氢气体便逸不出来了,就形成了气孔。二是由于停弧过急形成了气孔。
4、气孔的防止措施
本人采用的方法就是“搅拌熔池法”。就是有规律的使焊丝(条)在熔池内摆动,设法破坏或延迟柱状体的形成,使氢气体顺利的逸出熔池金属,以避免气孔的产生,回焊法和“搅拌熔池法”有机的结合好,不仅能有效地避免裂纹的产生,同时也能有效的解决气孔的产生。
5、再热裂纹的防止措施:一是焊后外观检查没问题立即进行热处理。不能及时处理时应采取硅酸铝棉毡包扎缓冷的办法,时间不可过长,立即处理。二是严格控制好热处理中的升降温速度,不得超规范规定,特别是降温速度更不可过快。
五、焊后热处理
1、热处理工艺
焊后及时进行焊后热处理。电加预热宽度从对口中心开始,每侧不少于焊件厚度的三倍,且不小于100mm。电阻预热时升温速度按6250÷壁厚(℃/h)实行,且不大于300℃/h。热处理采用电阻加热方式,升、降温速度为≤180℃/h,恒温温度为720~750℃、降温速度为≤180℃/h,恒温温度为720-750℃,恒温时间根据管壁厚制定。热处理工艺曲线示意图见图2。
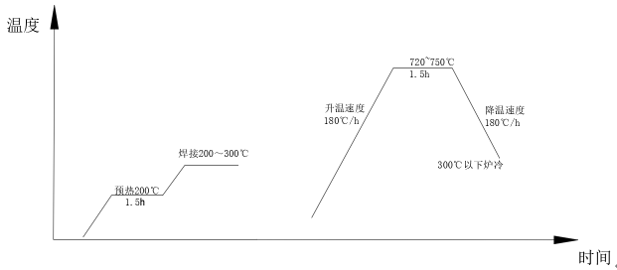
图2 热处理曲线图
2、热处理的保温宽度,从焊缝中心算起,每侧不小于管子壁厚的5倍,且每侧应比加热器的安装宽度增加不少于100 mm。
3、升/降温速度不大于200℃/h,降温过程中温度在300℃以下可不控制,在保温层内冷却至室温。
4、热处理时,应力求内外壁和焊缝两侧温度均匀,恒温过程中在加热范围内任意两测点间的温差应低于50℃。
5、热处理的测温必须准确可靠,应采用自动温度记录仪,采用K型镍铬电阻合金热电偶。热处理的测温必须准确可靠。进行热处理时,水平管道的侧点应上下对称布置。焊缝热处理后应做好记录和标记。
六、结论:
12Cr1MoV钢管焊接容易产生冷裂纹、再热裂纹、气孔等缺陷。检修中按照工艺施焊,并从操作技巧的角度总结了避免缺陷的一些措施,在实际工程应用中起到了良好的效果。在企业检修中锅炉小溢流管改造工程中12Cr1MoV钢管对接焊口22只,RT探伤结果:99%合格。实践证明制定的工艺措施可行,确保了检修过程中的焊接质量。
参考文献
1、焊工培训实用教材,北京:中国电力出版社,2001年。
2、机电工业考评技师复习丛书编审委员会编,电焊工、机械工业出版社出版。
3、《职业技能鉴定教材》、《职业技能鉴定指导》编审委员会、电焊工、李建三主编,北京:中国劳动出版社,1996年。
作者简介:王斌(1969-),男,江苏南通人,本科,高级技师,研究领域:机电一体化、焊接专业教学,焊接教研室主任。