奥氏体不锈钢中径管焊接工艺
摘要: 本文主要介绍SA213-TP304奥氏体耐热不锈钢中径管Ø159×7mm在焊接过程中存在的应力腐蚀开裂,焊缝成形不良所形成的缺陷和它们形成的主要原因,再根据焊接工艺评定,焊接工艺措施与实际应用中的效果,采纳的一些方法和措施。
关键词: 奥氏体不锈钢;焊接缺陷;解决方法
中图分类号:TG156.92;TG142.71 文献标志码:A
前言:在检修焊接过程中经常遇到SA213-TP304奥氏体不锈钢的材料。SA213-TP304奥氏体不锈钢是美国试验材料协会标准(ASTM)用钢。主要用于锅炉过热器、再热器、化学补水管道等部件。在实际焊接工作过程中,发现焊缝根部易出现类似于未焊透的根部缺陷,这种所谓的未焊透实际上是合金元素的氧化、烧损造成的,在焊缝根部位置处,可发现有起皮问题,于此同时,金属组织表面具备松疏性特征。实际焊接环节,焊丝与母材熔合得比较困难。焊缝易有明显的如焊丝头状的夹渣物存在。本文具体分析了奥氏体不锈钢的焊接性能,改进了焊接工艺,焊后对焊缝进行外观检查没有发现裂纹、根部烧损、气孔,夹渣等缺陷。经历多次采用本方法施焊SA213-TP304钢外观质量取得了良好的效果。
1 奥氏体耐热不锈钢焊接时存在的主要问题
SA213-TP304奥氏体耐热不锈钢的主要化学成分见表1。
表1奥氏体不锈钢的化学成分%
钢 号 Cr C Ni P Si S Mn
SA213-TP304 18.00-20.00 ≤0.08 8.00-11.00 ≤0.045 ≤1.00 ≤0.030 ≤2.00
1.1 有产生焊接热裂纹的倾向
由于奥氏体不锈钢导热性差,其电阻率是低碳钢的4倍;线膨胀系数大,约是低碳钢的2倍,这种情况下,当焊接局部发生冷却及加热情况时,会造成焊缝结晶,最终在较大拉应力的作用下,形成裂纹;此类型材质中会还有较多杂质,如硫、磷以及镍等,这些杂质元素在熔池中会产生新的共晶体,故含Ni量越高,则越容易产生热裂纹问题;这一类型的材质固相线及液相线通常存在较大的距离,不容易结晶,同时奥氏体结晶由于存在较强的枝晶方向性,因此会存在较严重的杂质偏析问题。以上原因的存在,使得奥氏体不锈钢容易产生裂纹。
1.2 晶间腐蚀及475℃脆性
奥氏体不锈钢众多破坏形式中,晶间腐蚀是极其危险的一种,它的特点是沿晶界开始腐蚀,从表面上看一般不容易发现,但它使受力管道焊接接头的机械性能显著下降,并且容易发生早期破坏,根据“碳化物析出,造成晶间贫铬理论,在450—850℃(范围内C和Cr易在奥氏体晶粒边界产生碳化铬,使得晶粒边界局部贫铬,晶界处的铬下降到12%以下,使得耐腐蚀性下降。此外,如奥氏体不锈钢焊缝长时间处于450~850℃环境状态下,很容易形成硬脆(HRC﹥60)金属间化合物。因为这种化合物的存在,阻断了晶间的联系,大大降低了该位置处的韧性以及塑性,同时抗晶间腐蚀性能也有所下降,也即475℃脆性。
1.3 焊缝成形不良产生原因
焊接过程中,焊缝中会存在较多的合金元素,降低了熔池的流动性,这是焊缝成形不良主要原因。这种情况下,根部位置处盖面焊道表面较为粗糙并且焊道的背面位置也成形较差。常温以及高温工况下,这一问题不会对焊缝性能产生明显的影响,不过在低温工况下,会出现应力集中问题,严重影响了焊缝性能质量。
1.4应力腐蚀开裂
产生该类型裂缝的主要原因为:特定腐蚀环境下,焊接接头受到拉伸应力影响进而出现开裂问题。应力腐蚀开裂主要发生位置是焊接接头位置,因此是较为严重的一种失效形式,具体表现形式为脆性破坏,不会发生塑性变形现象。
2 奥氏体不锈钢的焊接工艺要点
SA213-TP304奥氏体耐热不锈钢的焊接要比珠光体耐热钢(12Cr1MoV)等钢的焊接复杂得多,这是因为焊接时不仅考虑焊接接头的一般强度问题,而且还要考虑焊接接头需具有的特殊性能,主要是抗晶间腐蚀能力,高温强度,以及抗氧化性能等。同时还要注意防止焊接过程中出现4750脆性。这些因素给SA213-TP304焊接带来一定的困难。
2.1 正确选择焊接材料
根据奥氏体不锈钢焊接的主要问题,需要正确选择焊接材料,可以选择超低碳焊丝或者焊条,主要是由于晶间腐蚀会随着含碳量的升高而增大,因此,通过降低焊缝含碳量可有效防止晶间腐蚀问题的发生,可在一定程度上提升焊缝耐晶间腐蚀能力。当奥氏体中溶解的碳≤0.03%时,不会产生碳化铬,因此,通常会保证焊丝碳的含量不超过0.04%,这也是超低碳的关键标准。在超低碳焊丝的良好应用下,有效控制了贫铬问题的发生,并且为对敏化温度区间范围进行控制,使用钨极氩弧焊打底,自然就提高了焊缝抗晶间腐蚀的能力。
2.2 焊接注意事项
根据上述不锈钢的焊接特点,为保证接头的质量,防止焊缝成形不良,应力腐蚀开裂,焊接工艺如下:
焊前准备。清除各种污染,尽可能降低焊缝金属增碳现象的出现。焊接工作开展前,选择酒精或者丙酮去除焊接区及破口位置出的油及水,注意不可应用碳钢钢丝。利用砂轮等工具进行除锈及清渣操作,避免强制组装,必须采用合理的成形加工和组装工艺,合理选择焊材,使焊缝与母材应有良好的匹配。
第二,选择小的线能量,同种条件下,会减少10%至20%的焊接电流。
第三,实际焊接环节,需要将焊件层间温度控制在150℃以下。焊接不锈钢厚板过程中,可利用压缩空气吹焊缝表面,或者采取焊缝背面喷水的方式,达到加快冷却的目的,不过需要做好层间清理工作,以免对焊接区产生污染。
第四,选择窄焊道技术进行焊接操作,焊接环节将焊丝固定住,确保融合质量的同时,提升焊接速度。
第五,除了以上的注意事项,还应着重注意以下内容:最后焊接接触介质的焊缝;避免飞溅;为防止接头背面氧化同时保证良好成形,应对接头背面加氩气保护;焊缝表面应光洁无杂质,不能存有残渣;焊缝交接处应错开;不可随意打弧;工件上的焊接电缆卡头要卡紧;应保证焊缝根部焊透。
3 具体焊接工艺参数与方法
对接焊选择的焊接方法为手工钨极氩弧焊打底,手工电弧焊盖面。因为根部采用手工钨极氩弧焊比手工电弧焊打底质量好,效率高,变形小的优点。此外氩弧焊保护效果好合金过渡系数高,焊缝成分均匀而且稳定。
3.1 焊前准备
(1)采用奥氏体不锈钢专用焊丝H0Cr19Ni9Ti(规格ø2.5mm)氩气纯度为99.99%,直流正接电源。
(2)氩弧焊焊接场地需要做好防风、防雨雪等工作,以确保氩气保护效果。
(3)检查氩气流量计橡胶皮管有无损坏,焊件在组装前,需要保持焊口表面及两侧一定范围内的清洁干净,去除其中杂质。
3.2 背面充氩保护
SA213-TP304钢在手工钨极氩弧焊打底时,应进行焊缝背面充氩保护,确保背面成形良好,避免氧化、烧损问题的出现。充氩保护时,焊缝内壁采用可溶纸等粘贴在坡口两侧距离200~300mm的管子内,使之形成小的气塞,堵住空气的流动。然后在该小气室内进行充氩,这样有利于保护焊缝根部和节约氩气,最好采用ø3~ø5mm的微细不锈钢管固定在氩气皮管的输出接头上。将不锈钢管砸扁但不能堵塞,在两边缘磨成几个缺口,使氩气分布均匀(图1)。
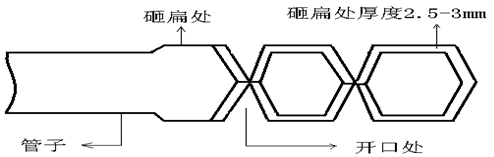
图1 充氩保护装配示意图
然后将细微管通过焊缝的对口间隙伸进去打开氩气开关,将氩气流量调到15-20L/min对焊缝根部进行充氩保护(图2)。
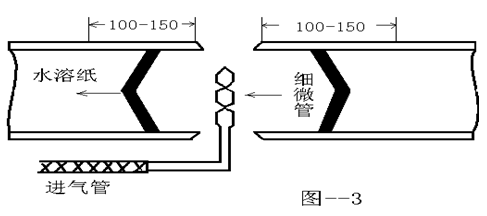
图2 充氩保护示意图
3.3 定位焊
SA213-TP304奥氏体不锈耐热钢的导热系数小,而膨胀系数大,在自然状态下焊接时易产生焊接变形,如在焊接时定位不牢固,就可能因焊接变形而导致坡口间隙缩小严重时,甚至没有间隙就会造成管口焊接时经常出现未焊透的一个主要原因。因此,在定位焊时不能按照常规点焊两点,应该沿管子四周均匀点焊4点,各点长度保持在5~10mm范围内,通过这样的方式才不会使对口间隙变小。
3.4 焊接过程快速冷却
为避免SA213-TP304钢在焊接过程中可能发生475℃脆性而产生裂纹。焊后或焊接环节可直接浇水或用湿毛巾进行冷却,由于奥氏体不锈钢冷却环节不会存在马氏体相变,因此,不会出现淬硬组织。
3.5 填丝方式
氩弧焊打底时,焊丝填加最好选用断续加丝法。电焊盖面时最好选用连弧焊,小线能量,小电流,小摆动,快速焊,焊条选用E347-16(A132)。见表2
表2 SA213-TP304母材与焊材成分对照表
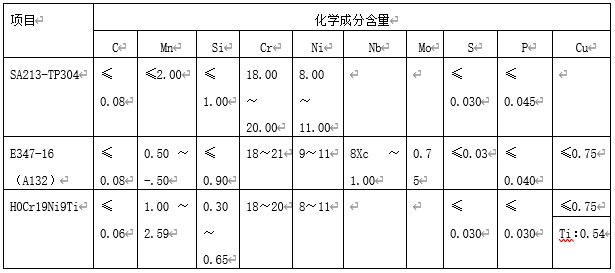
3.6 焊接工艺参数
实际焊接过程中涉及到的焊接工艺参数如表3所示。
表3 焊接工艺参数表
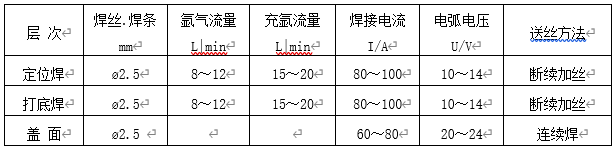
4 操作技巧
(1)焊接过程中焊丝不能与钨极接触或直接深入电弧的弧柱区,否则造成焊缝夹钨和破坏电弧稳定燃烧,焊丝端部不得抽离保护区,以避免氧化,影响质量。
(2)填丝环节,不可扰乱氩气气流,并且在停弧时还要通过氩气保护熔池,从而避免焊缝发生氧化。焊后半圈时,电弧熔化前半圈仰焊部位,待出现熔孔时给送焊丝,前两滴可以多给点焊丝,避免接头内凹,然后按正常焊接。
(3)焊到12点收尾处,暂停给丝,用电弧把斜坡处熔化成熔孔,收口后再将电弧后移加丝焊接,保证焊缝的宽窄差和高低差。注意焊到后半圈剩一小半时,需要减小内部保护气体流量,具体数值是3 L/min即可,起到防止气口或使焊缝形成内凹的作用。
(4)焊条电弧焊焊接时采用小线能量,小电流快速焊。焊条不可出现横向摆动现象,焊道不宜过宽,应尽可能的降低宽度,保持在焊条直径3倍宽度之下。相同条件下,与低碳钢焊条相比应降低20%左右的焊接电流值,通常保持在焊条的25~30倍之间即可。小线能量应用下,会有较快的冷却速度,不会在敏化温度区停留较长时间,可起到防止晶间腐蚀的作用;由于小线能量热输入小,并且焊接应力也较小,会有效防止热裂纹以及应力腐蚀问题的发生。此外,因为焊接电流较小,会防止焊条药皮开裂,也会避免焊条药皮发红问题的出现。
(5)焊接层间用机械清理,打磨出金属光泽。收弧采用断续收弧,以防止产生弧坑裂纹及缩孔。焊后可应用强制冷却的方法,从而有效缩短敏化温度区停留时间,最终避免晶间腐蚀问题的出现。
(6)实际焊接过程中,不可进行后热以及预热技术手段,不可降低焊后冷却温度。若焊接处理涉及多层多道,应注意保证各层道间温度不超过150℃。
5 结论
本文主要讲述了SA213-TP304奥氏体耐热不锈钢在实际工作焊接时有产生热裂纹、晶间腐蚀和475℃脆性、应力腐蚀开裂、焊缝成形不良、根部烧损、气孔、夹渣等缺陷。通过合理选择焊材采取合适的焊接工艺,合理定制成形加工和组装工艺,焊缝的背面充氩保护,焊口及母材内外壁清理干净,采用较小的焊接线能量进行快速焊接,基本解决了上述的焊接过程中出现的问题。本套工艺在多个项目中应用取得了良好满意的效果。
参考文献
[1]葛兆祥.焊接工艺及原理[M].北京:中国电力出版社,1997.
[2]钱昌黔.耐热钢焊接[M].北京:水利电力出版社,1988.
[3]焊接工艺评定规程:DL/T868—2004[S].
作者简介:祝春兰(1977—),女,本科,江苏海安人,高级实习指导教师,主要从事焊接理论教学工作。