588板簧支座加工工艺改进
摘要:588板簧支座零件是汽车起重机上四大关键件之一,相比其他三种关键件的配套能力,它的配套能力需要进行大幅的提升,以适应整机的生产需求。588板簧支座生产周期较长,原有的工艺流程较长,工序较多,形位公差要求较高,需要人为找正,加工时间长、周转周期大,且不能有效控制588板簧支座的加工精度。没有有效的测量手段对毛坯料、成品件进行测量检测。所以现阶段根据企业现有生产设备改进588板簧支座的加工工艺,提高加工效率,在保证产品质量的基础上对刀具进行国产化替代,降低生产成本,同时还要采用行之有效的措施降低工人劳动强度。
关键词: 板簧支座 工艺改进 国产替代
一、588板簧支座工艺分析
588板簧支座毛坯为铸钢件,铸造成型后在进行机械加工,其铸造尺寸与现有工艺要求存在较大的差异性,影响后续的加工,对机床与刀具都会产生较为严重的损坏。其形状较为复杂,外观看是一个小板凳的形状,属于异形零件,加工部位较多工艺复杂,需要多次装夹完成零件的加工,对工装的要求较高。并且该零件铸造成型后表层存在一层硬皮,极易对刀具产生较大的损害。目前对该零件的生产和加工大多采用是进口山特维克刀具,数控刀具的费用成本较高,亟需将数控刀具进行国产化的替代降低生产成本。
二、588板簧支座加工要点
1.尺寸精度要求较高
根据图2-1和图2-2所示该零件的加工精度普遍在7级和8级精度。如果仅仅是单件的加工对于使用加工中心这样的高精度设备来讲不是什么困难的事情,但对于大批量的生产情况下保证每个零件的加工质量是较为困难的,这对于机床以及刀具的稳定性都提出了较高的要求。因此,为保证每个零件的加工质量,对尺寸精度高的进行半精加工,根据检测结果进行精加工,通过这样的方式加工精度就会得到很好的控制,但是如果每一个尺寸都这样处理的话加工效率就明显降低,因此在设定加工工艺的时,要将同一把刀具所进行的各尺寸精加工,留有相同的加工余量,只检测一个半精加工尺寸,调整零件精加工余量,同时控制所有的加工尺寸。
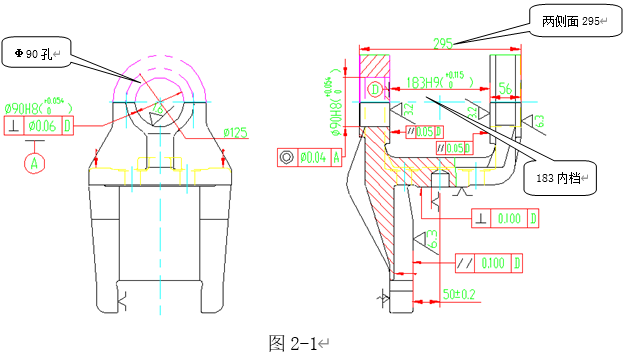
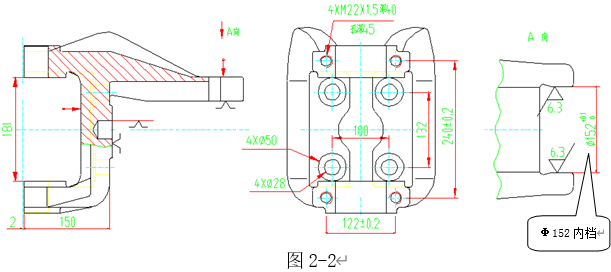
2. 形位公差尺寸的控制
根据图2-3所示,该零件需要控制的形位尺寸共有6个,是一个复杂异形零件,加工过程中容易引起加工变形,形位公差精度不容易控制在公差范围内。
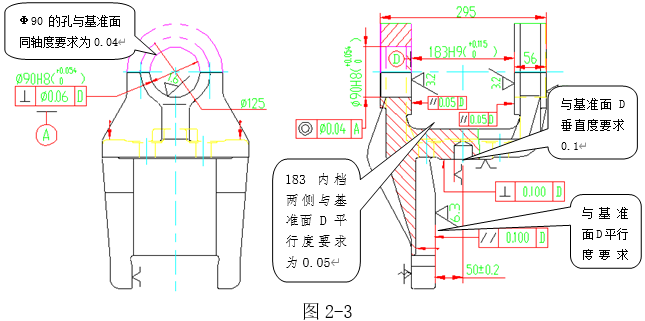
三、588板簧支座零件生产过程中出现的问题及解决措施
1.加工效率低产能不足,工序分散,转运效率低
首先588板簧支座零件工艺流程复杂,需要刨、划、铣、镗、钻、攻六道加工工序才能完成零件的加工;其次该零件需要进行多次装夹,其形位公差尺寸难保证;再次加工工序较为分散,造成零件加工时间较长;最后零件的加工需要进行多次转运,人员劳动强度大,造成不必要的浪费。通过对零件加工过程中上述的原因进行分析,提出了如下解决措施
(1)工艺优化
将原来零件加工六道工序全部改为在卧式加工中心上进行生产加工,把工序集中起来,通过一次装夹完成零件加工,提高零件加工效率和零件的重复定位精度,保证了零件加工精度,降低了工人的劳动强度。
(2)工装优化
设计制作卧式加工中心专用工装,如图2-4所示,以底面作为支撑平面,后面用限位块限制零件的前后运动,上面用压板对零件进行夹紧,两侧各制作一个限位,增加了两个辅助夹紧装置,提高夹具的刚性,使加工零件能够通过一次装夹完成零件的加工。
(3)程序、刀具参数优化
在数控机床上加工零件时,加工参数都预先编入程序。在零件加工过程中,通过速率调节旋钮调整切削用量,因此程序中选用的切削用量不是最佳的、合理的切削用量。所以通过大量的实验和数据的积累选定了最为合适的切削用量来进行加工,保证了加工的效率和加工的稳定性。而切削参数的选择对加工质量、加工效率以及刀具耐用度有着直接的影响。其次是加工程序的优化,由于毛坯的制造误差较大,造成零件加工过程中,铣面加工第一刀加工余量差异性较大,当切削深度较大时极易造成铣面刀具的损坏,因此在零件装上工作台之前应进行一个预测量,根据实际加工余量调整加工程序。铣面粗加工程序如下:
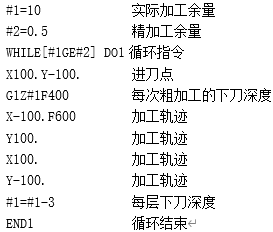
其中#1为铣面加工余量,每次加工前根据毛坯的实测值进行调整。
2.国产刀具替代进口刀具,刀具自制和刀片的二次利用
现阶段为保证产品质量和加工效率,对于588板簧支座零件的生产加工基本上采用了山特维克进口刀具,刀具费用高,花费成本较大,为解决此问题特从以下两方面进行改进。
(1)国产化替代
由于近几年国产刀具的生产质量也有了较大的进步,部分刀具达到了该零件的加工要求,满足了切削该零件的使用性能,虽然在刀具耐用度方面仍有一些差距,造成刀片磨损更换频次快,但总体的加工效率依然能保证,大大地降低了刀具成本。
(2)数控刀具自制、废旧刀片二次利用
加工该零件时,加长数控刀具需要定制生产,成本极高,通过自己设计和制作刀体,安装上原厂刀片,依然能够满足加工要求,节省了较高的购刀成本。
部分数控刀具刀片在使用过程中,有两个刀尖损害后,已经报废。为能利用报废刀片的另外两个刀尖,重新设计和制作刀体,虽然加工效率有了一定的降低,但是通过废旧刀片的再次利用节省了大量的成本。
四、588板簧支座加工工艺改进后的效果验证
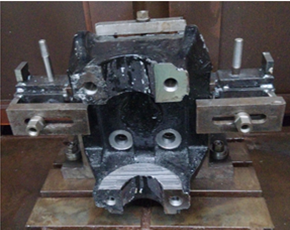
588板簧支座零件在经过工艺优化,工装优化以及程序刀具参数的优化起到了明显的效果提升。首先是效率的提升,单件加工周期降低明显,单件加工周期由从改进前的60件/min降低到现在的44.8件/min;其次是零件加工质量的提升,零件加工精度效果稳定,在全年的生产过程中没有出现一个废件;最后是加工成本的降低,仅是通过国产化替代措施,经过核算刀具成本节约为10万/年。按年产2万台计算,年降本约20000*20*2=80万元。
参考文献:
[1] 孙丽媛主编 机械制造工艺及专用夹具设计指导[M] 北京:冶金工业出版社2002,12
[2] 李庆寿主编 机床夹具设计北京[M] 机械工业出版社1983,4
[3] 赵志修主编 机械制造工艺学北京[M]机械工业出版社1984,2
姓名:张春梅 ,出生年月:1983年12月5日,性别:女,民族:汉,籍贯:江苏,单位:南京工业职业技术大学,职称:一级实习指导,研究方向:数控加工。