风电叶片液压模具翻转控制分析
(江苏省常熟职业教育中心校,江苏苏州 215500)
摘要:为对大型风电叶片模具液压翻转系统中的缺陷进行完善和克服了,基于矢量变频-液压调速,通过科学控制对象的选定,运用模糊-PID复合控制器控制模具翻转过程,通过相应模型的建立,并对其进行仿真,根据仿真结果改进控制器参数,评价翻转系统。相比较于液压调速,电机调速反应灵敏度不高,因此增加成本,降低整体的动态性能。本文通过分析风电叶片液压模具翻转控制效果,旨在为有效改善风电叶片液压模具翻转系统的控制情况提供参考。
关键词:液压翻转;风电叶片;同步性
中图分类号:TM614;TP273 文献标志码:A
风力发电以基建周期短、装机规模灵活以及清洁可再生能力在我国发展十分迅速。风力发电叶片将风能转化为电能,以巨大蕴量保证发电系统的正常运行。随着经济水平的增加,对风力发电装机功率和叶片尺寸的要求也越来越高,因此需要大型的风电叶片模具。大型风力发电机位叶片模具长度在七十m以上,因此对翻转系统翻转同步稳定性和承载负荷能力的要求也更加严格。目前传统行车机械式翻转系统对于大型风力发电叶片模具的要求已经难以满足。当前以PLC控制比例开口度对油泵输出油量进行调整,从而控制三个或以上的翻转臂液压翻转系统,这种方式为目前国内外普遍采用的方式。这种方式因为模具长度较长以及模具自重较大,因此在翻转过程中以及模具开合过程中对翻转臂的同步性产生一定影响,严重影响模具的使用期限。本次文章对基于变频电机实施闭环调速的多翻转臂液压自动开合模控制系统进行介绍,基于多翻转机构系统,对翻转机构的翻转油缸工作原理进行分析,对液压电气系统进行改进和设计,采用PID闭环控制模式,对翻转过程中翻转角度同步性和平稳性等难题进行有效解决[1]。
1 液压翻转系统的工作原理和结构
1.1翻转系统结构
翻转结构包括翻转油缸、支撑油缸、旋转机架、固定机架、旋转中心轴;风电叶片模具构成包括固定面和运动面,也就是背风ss面和迎风ps面,多个液压翻转机构架和模具分别实施刚性连接。
1.2翻转系统工作原理
分析其中一个翻转机架结构。如图1所示:
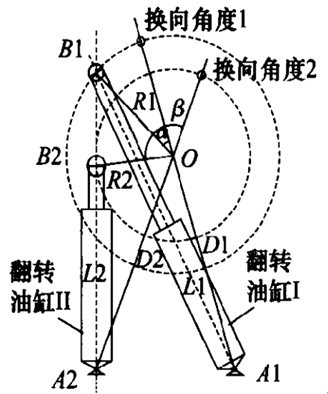
图1 换向点计算示意图
图1中液压翻转油缸II和I下方的铰接点通过销轴连接与翻转机架底座固定部位,液压翻转油缸2和1上处的铰接点翻转机架可翻转,a1、b1、a2、b2分别为其对应位置。o表示液压翻转机翻转部位的中心轴,d1为液压翻转机固定部位铰接点与o之间的距离,d2为翻转机架中心轴与o之间的距离,r2、r1表示翻转机架可翻转部位与液压翻转油缸和中心轴的距离。L2、L1表示翻转油缸下部到上部铰接点的距离。模具翻转期间,液压翻转机架需要经过两个奇异点xy,翻转油缸1还没有经过奇异点x时,油缸2和1伸长的翻转需要通过翻转机架,到达后,油缸1有杆缸杆长度最大化,翻转结构凭借油缸2有杆腔缸杆推动从而实施翻转,带动油缸1经过奇点实施换向动作。后续过程中油缸1一直进行回缩动作。油缸2经过y奇异点前,其有杆腔缸杆实施伸长动作,到达后,油缸2有杆腔缸杆达到最大长度值。凭借油缸1尤刚强拉动,翻转机架实施翻转动作,带动油缸2进行换向动作。伺服油缸均进行回缩动作,到模具打开完全到位[2]。
2 控制系统设计
操作系统期间,有两种方式可对系统进行控制,分别为触摸屏控制和遥控器控制,有效解决了无线遥控系统由于电磁干扰原因导致其难以应用的状况。根据相关步骤进行开模,使信号进入PLC中,接通之后油泵启动,模具翻转开始。PLC自动检测翻转期间传感器信号,计算其平均角度值,如果某一翻转机架角度值没有大于平均值,PLC会针对比例对4-20mA电流信号进行计算,自动追赶对应变频器输出频率,另外,如果某一翻转机架角度值超出平均值,需要降低对应变频器的输出频率[3]。
开模翻转的整个过程将电磁换向阀动作分段,具体如下。第一阶段:模具合模后翻转到翻转油缸和机架经过第一个x奇异点。PLC输出信号通过电磁阀线圈ya11、ya9、ya7、ya5、ya3、ya1的接通,对三位四通电磁换向阀进行打开,利用油泵和电磁换向阀将液压油液传送到翻转油缸无腔杆,翻转油缸从1到6均实施伸长推动ps面模具翻转运动向上。第一个x奇异点有翻转油缸经过时,PLC对ya5、ya9、ya1电磁阀线圈进行关闭,对ya10、ya6、ya2电磁阀线圈进行接通,
这时候翻转油缸一、三、五均出现变化,液压油液换向通过电磁换向阀,进入渠道从之前的无杆腔变为有杆腔,油缸进行回缩动作。翻转油缸二、四、六对应的电磁阀线圈动作与原来相同,油缸缸杆伸长,带动油缸一、三、五经过奇异点。第二个阶段为在第二个y奇异点与第一个x奇异点的翻转油缸运动。第一个x奇异点经过之后,油缸实施换向动作,经过第二个y奇异点,PLC将ya一、ya七、ya三线圈的输出信号进行关闭,接通ya十二、ya八、ya四。这时翻转油缸二、四、六动作出现改变,液压油液进入渠道从原无杆腔,换向利用电磁换向阀,变为进入渠道为有杆腔,伸长油缸动作变为回缩,翻转油缸一、三、五对应的电磁阀线圈动作与原来相同,油缸缸杆进行回缩动作,带动翻转油缸二、三、六经过奇异点。第三个阶段为翻转油缸经第二个y奇异点后,ps面模具开模。该时期模具从原本是阻力的自身重量变成动力,油缸均实施回缩动作,具有一定压力:确保PS面模具下落速度平缓[4]。
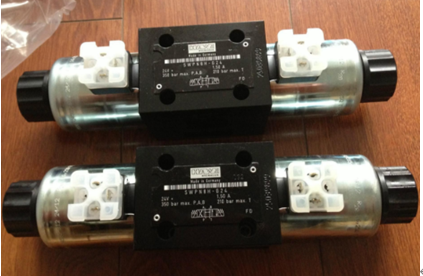
图2 电磁换向阀
仿真电气环节和综合液压,当翻转角度为零度时,稳态误差小,无超调,响应时间在一秒左右。随着翻转角度的逐渐增加,消除角度误差的能力也在逐渐降低,稳态误差加大,响应速度变慢。基于翻转速度不变的状况下,翻转架在不同时间里的旋转角度也不相同,因此在PID参数相同的情况下,如翻转机架位置和工作状况出现变化,短时间内模具难以满足工作需要,还会造成停工。因为系统会被负载等因素所影响,因此在某些时间段中,会导致系统工作发挥不出好的效果。因此,现下使用的液压翻转模具不管怎么样对PID参数进行调节,每个时间点均会出现一定程度的位置误差,不管误差的范围是否在要求之内,均会进行自我调节,这种情况会导致调节现象会频繁出现在翻转过程中,导致厂家在使用模具时反映轻微颤抖现象出现在整个运动过程中。出现抖动的原因主要是因为系统液压压力造成冲击产生,从本质上来说包括2点:①电磁阀组通断逻辑发生变化;②当翻转机构的翻转重心和负载超过了旋转中心,负载重力就会发生变化,从翻转阻力变为翻转动力,油缸从伸长转变为回缩时,液压系统会被巨大的外界压力产生冲击,致使系统出现严重抖动。要想消除抖动,需要降低外界对其的压力冲击,因此将比例压力阀cs加入控制系统中,可有效调节系统压力,使其能够保持平稳运行。抖动的消除显著改善了翻转系统正常工作中的平稳性,在系统设计方面具有重大意义。
独立、分开控制翻转过程的三个阶段,每个阶段的控制对象都设定为液压缸a和b的伸长回缩量的总和。等流量伸出量为液压缸缩回量等效、传感器检测液压缸行程。翻转架进行的每一次活动都与一组行程数据对应,对其发展至非线性环节的情况进行有效避免,而且通过模糊-PID复合控制器控制翻转机架的活动过程,因为存在的控制死区,在误差不明显时没有出现动作。有效对频繁调节现象进行改善[5]。
翻转架在零0°、30°、70°时,误差阶跃响应均不存在超调,响应速度高达0.45s,要求得到满足,角度位置不会对系统的品质产生影响。由于角度不同出现的变化是因为不同时刻,形成误差想角度误差的转化系数也不相同。因此,可有效改善控制系统中的响应特性。基于翻转过程的特点,对其实施分段控制。整个阶段内所有时刻的翻转支架液压缸行程与匀速翻转要求的理想行程几乎全部对应,这说明控制系统可对翻转架的匀速翻转进行实现。
3 效果分析
实际翻转中模糊-PID复合控制控制系统可对各翻转机架角度误差进行控制,对之前大型风电叶片模具翻转过程中角度误差明显的问题进行有效解决。另外因为各翻转机架回路系统中电磁溢流阀y一、y二、y三的增加,翻转油缸经过xy奇异点时,可对换向产生的冲击进行缓解,确保模具翻转过程中的无抖动、速度平稳。翻转油缸进油口和出油口全部增加双向平衡阀,中断系统操作,如果翻转过程中出现意外情况,具自主降低。该系统具有自动停机报警功能,但电气控制系统出现故障,或者液压系统出现故障,造成各翻转机架误差变大难以进行自动补偿追赶时,该功能就会启动,防止由于故障发生导致模具应力受损等严重事故[6]。
4 结束语
在风电模具翻转液压系统中应用模糊-PID复合控制器和变频调速技术,可对液压多架翻转系统不平稳转动难题进行有效解决,另外还显著降低同步误差,将其控制在零点二度以内。模糊-PID复合控制器和变频调速技术在国内已经开始应用,根据应用企业的使用效果,可看到叶片生产质量得到显著提升,同时还提升了模具的使用期限,对风电模具翻转液压系统中应用模糊-PID复合控制器和变频调速技术进行研究探讨具有重要的实际应用价值和理论意义。
参考文献
[1] 石鹏飞.大型风电叶片模具翻转系统设计研究[J].机械研究与应用,2018, 31(5):37-40.
[2] 吕玲.风电机组液压式风轮锁卡死故障分析及对策研究[J].机床与液压,2019, 47(8):197-199.
[3] 武玉柱,孙文磊,周建星.风电机组行星传动柔性齿圈变形特点分析[J].机床与液压, 2019,47(20):98-103.
[4] 李毓洲,仇明,张永康,等.超大型风电安装船液压升降系统结构件有限元分析[J].船海工程,2020(4):37-39.
作者简介:郁蔚(1982—),男,江苏常熟人,本科,讲师,主要研究方向为模具、PLC液压与气动自动化控制、机械结构设计与装调。